Hawkins has investigated many cases involving failures of steel structures. Our knowledgeable and experienced team of forensic investigators can establish the cause of a failure by either a detailed desktop study or site investigation, in addition to reviewing the relevant documentation and carrying out numerical back-analysis. Click here to read part one of this article if you would like more background information.
The Hawkins Built Environment team has found that although failures can be caused by either errors in the design, or errors at the construction and execution stage, most failures are often caused by a combination of both.
CASE STUDY 1: COLLAPSE OF A STEEL PORTAL FRAME
Following a storm that affected most parts of the UK, Hawkins was instructed to investigate the cause of the partial collapse of a steel portal framed structure that was under construction.
Photo above: Partially collapsed portal frame, which used to be part of a factory building
The portal frame comprised steel columns and pitched rafters, connected by moment-resisting welded connections. Hawkins carried out both a detailed inspection of the structure, and a review of the design of the structure, and found that the design was adequate. We then carried out a thorough review of the original construction sequence proposal and the sequence of actual construction, to establish whether there were any deviations from the intended sequencing of the works.
Witness accounts, site records, and the site investigation indicated that permanent cross bracings had not been fully installed before the construction of adjacent bays. Hawkins carried out calculations and analysis to assess the load carrying capacity of the structure without the full bracings. The results showed that the portal frame, as constructed, was weak and would fail in the event of high wind loading. In this case, the contractor also failed to use temporary bracings, which should have been provided in order for the structure to withstand wind gusts, as well as to stabilise the structure until permanent bracings were installed. Further investigation revealed that there was no qualified site engineer on site performing a supervisory role for the contractor.
This case highlights the importance of proper site supervision and risk assessment during the construction of steel structures. If proper site supervision and risk assessment had been carried out, it is likely the sequencing of the works would have been revised and temporary bracing would have been provided.
CASE STUDY 2: FAILURE OF A ROOF CANOPY
A large warehouse roof canopy failed after a period of heavy rain. Hawkins was instructed to establish the cause of the collapse, and in particular whether the failure was caused by defects in either design, construction, or a combination of the two.
Our investigator attended the site within 24 hours of the incident. The single-pitched roof canopy consists of rows of trusses made of thin, galvanised cold-rolled steel sections. The roof had deflected so much that it landed on a heavy goods vehicle. Our investigation revealed that the design of the canopy had numerous deficiencies, with the most significant ones being the insufficient capacity of the diagonal truss members, as well as insufficient slope of the roof. Our failure back-analysis showed that the diagonal members were inadequate given the intensity of the rain, causing the truss to sag overall. Because the roof pitch was too flat, a slight sag of the truss would have allowed water to accumulate on the roof, thus increasing the load. The increased load led to further deflection of the truss, eventually causing the failure.
Following on from our involvement, the client asked that we review the design of their assets worldwide.
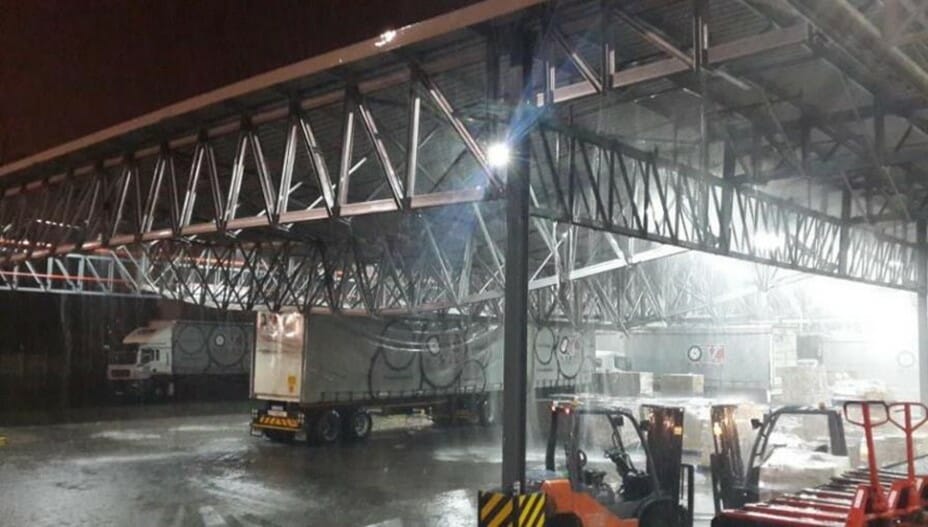
CASE STUDY 3: BUILDING COLLAPSE
Hawkins was instructed to investigate the cause of a sudden collapse of an office building that was under construction. The building consisted of a four-storey steel frame structure. When Hawkins visited the scene, most of the remaining steel frame had already been brought down by the demolition contractor, and the main steel truss was half buried in the debris.
Hawkins examined all the joints of the truss at the Health & Safety Laboratory where the main truss had been transported to and temporarily stored. At one joint, the end of the diagonal member had been welded to the flange of a haunch. The fracture surfaces of the haunch joint indicated the mode of failure was purely ductile rupture caused by tensile overload.
Hawkins carried out an investigation using Finite Element Analysis (FEA) software to determine the likely tensile capacity of the haunch joint. The results showed that the web of the haunch was grossly under-designed and that its tensile capacity was much less than the forces it would be required to carry. Our investigation revealed that the collapse of the building was caused by the poorly designed haunch joint that was incapable of carrying the forces applied to it by the diagonal truss member.

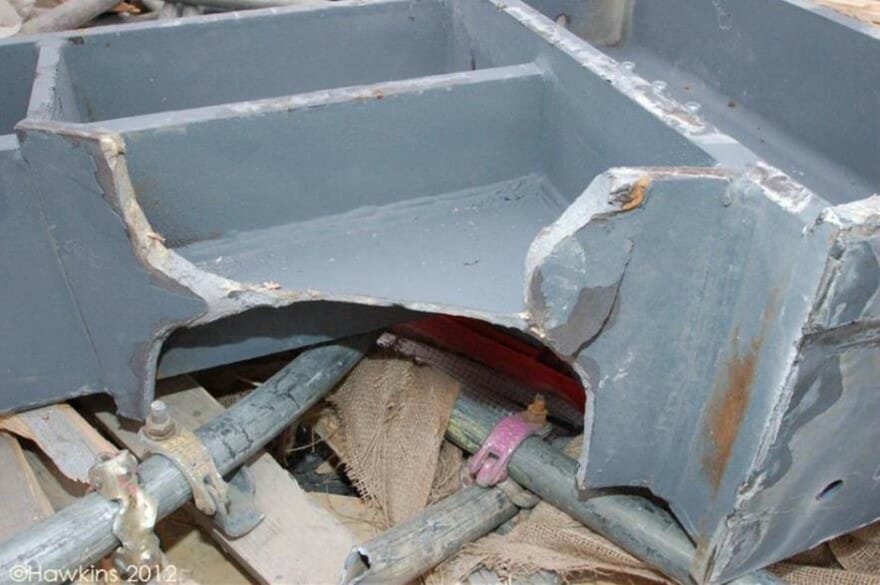
CASE STUDY 4: POST-FIRE INSPECTION OF STEEL STRUCTURES
A fire broke out in a manufacturing plant that damaged five conveyors. Hawkins was instructed to carry out a post-fire structural assessment of the steel roof beams that had been located above the fire. We attended the site immediately, because a fast response was required to allow the repair and replacement of the conveyors to progress.
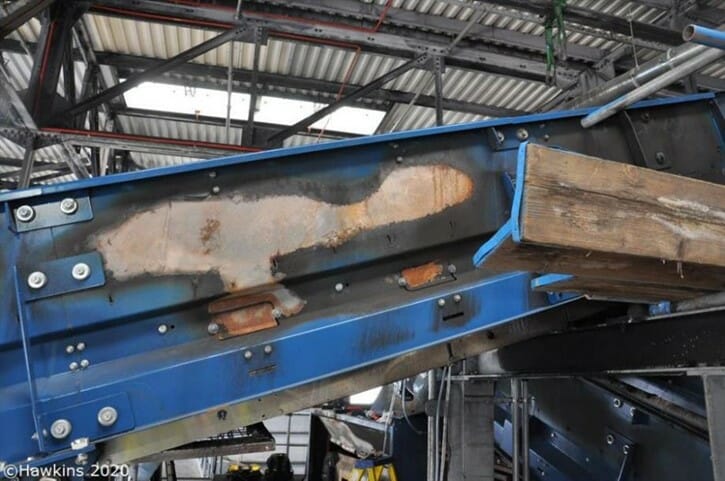
Our investigator carried out a visual inspection of the scene from a mobile elevated work platform. The visual appearance of the roof steelworks did not indicate any visible distortion or deformation. No obvious change in colour and no obvious soot deposits were observed on the roof truss. To verify the post-fire yield strength, we carried out calibrated hardness tests at various locations, such as on the roof beams and around the joints. The test results indicated that the post-fire yield strength of the steel elements was still satisfactory. We found that there was no evidence to suggest that the structural roof steelwork had been adversely affected by the fire. Hawkins provided recommendations to clean the conveyors including rust removal and re-painting of steel elements. Hawkins’ fast response enabled the client to get the unit back into operation as quickly as possible and gave them the confidence to continue using the plant.
CONCLUSION
Failures of steel structures are often caused by errors in both the design and the installation. Hawkins’ Built Environment team has investigated many failures of steel structures. Often these investigations are multi‑disciplinary, involving engineers specialising in geotechnical and material science. Our team of experienced forensic investigators provide quick response to failures to assist with stabilisation of the debris and preservation of important evidence. We offer comprehensive failure investigation including root cause determination, assessment of the extent of the damage, and development of rectification proposals. We adopt state‑of‑the‑art technology such as laser scanning and aerial photography to reconstruct the failure scene to facilitate investigation and communication with our clients.
While the probability of structural failure is low, the consequences can be severe. We provide risk management services by carrying out reviews of installation methods and designs to prevent collapses occurring in the first place.
ABOUT THE AUTHOR
Yang Dang is a registered Professional Engineer in Singapore with a background in structural design. Before joining Hawkins, Yang has over 10 years’ experience in the structural design of steel, reinforced concrete, precast concrete building in Singapore, Malaysia, and UAE. Yang specialises in investigating building defects and collapse, façade and cladding failures, and review of structural design.