Reinforced concrete is one of the world’s most widely used building materials. It is a composite material of concrete, which works well in compression, with metal bars, fibres or mesh embedded to provide tensile strength. Recent failures of structures containing Reinforced Autoclaved Aerated Concrete (RAAC) in the UK have garnered widespread attention. However, RAAC is just one form of concrete, and there are several other historical issues affecting existing concrete buildings. In this article, Jamie Paterson discusses how these issues affect the durability and life-expectancy of reinforced concrete buildings.
Reinforced concrete has many unique characteristics compared to other common structural materials. Most notably, the ability to readily alter its composition and form during design and construction.
Compositional changes can improve:
- Strength
- Curing time
- Water resistance
- Durability
- Shrinkage
- Buildability
- Embodied carbon content
Additionally, concrete has no fixed form allowing it to take-on virtually any shape. While this adaptability is advantageous, it also generates complexities that do not exist in other building materials.
Designing for Durability
Despite its robust appearance, reinforced concrete is vulnerable to deterioration caused by external factors such as moisture, chemicals, and extreme temperatures. The primary defence against these elements involves encasing the steel reinforcement behind a surface layer of concrete, known as “cover”. This protective layer must have sufficient thickness and be composed of a suitable concrete mixture. In the absence of suitable cover, harmful chemicals and moisture can infiltrate leading to corrosion. Furthermore, a lack of cover during a fire, results in the heating of the steel reinforcement and rapid strength loss.
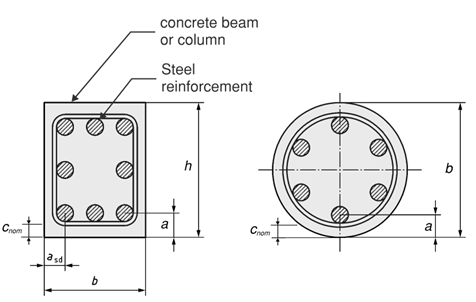
Cover requirement for fire (‘a’) and durability (‘cnom’) based on BS EN 1992
Identifying the minimum cover and mix design is typically a simple prescriptive process. However, it is critically important to understand the specific environmental and functional conditions that the concrete will be exposed to. The designer needs to be diligent in understanding all conditions that could affect the concrete, not simply the moisture levels.
In the presence of moisture, steel reinforcement will begin to corrode. The formation of rust on the surface of the steel exerts pressure on the surrounding concrete causing cracking and eventually spalling of the surface concrete. This, in turn, exposes the steel reinforcement to further deterioration. The process of corrosion is accelerated by the presence of certain harmful chemicals. These can enter the concrete during construction, via contamination of its constituent materials, or while in service. Improved industry knowledge and modern quality control measures have reduced the prospect of harmful chemicals entering concrete during manufacture and construction. However, many buildings that exist in the UK were constructed several decades ago and already contain contaminants.
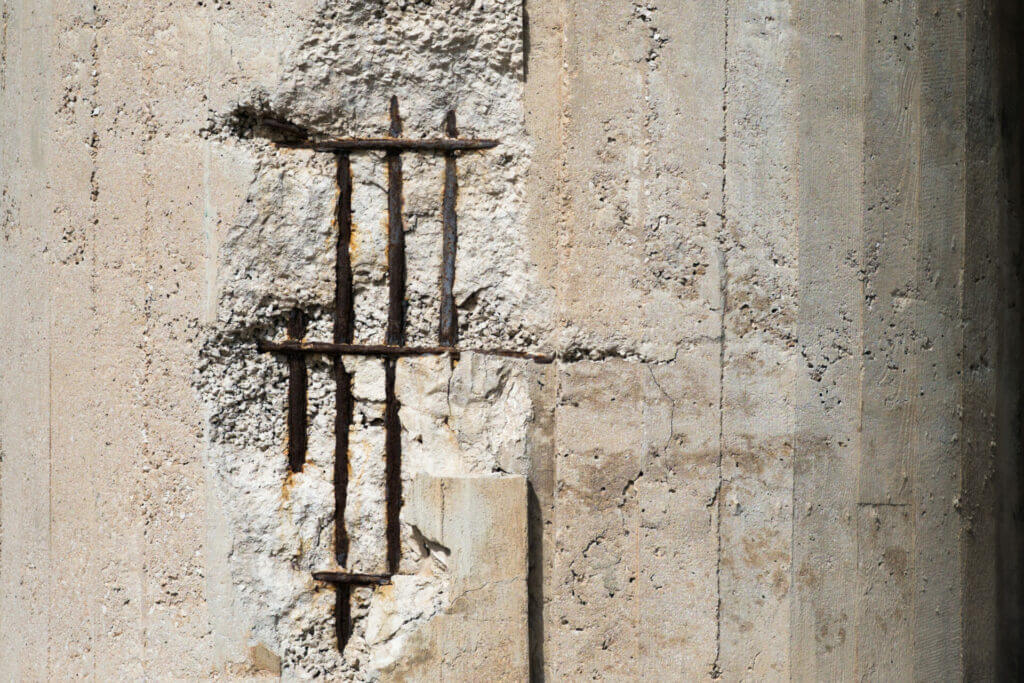
Historical Issues Affecting Concrete Durability
Cured concrete typically has an alkalinity of pH9 or greater, which provides passive protection to the embedded steel reinforcement. Over time, the alkalinity of cured concrete reduces, particularly at the surface, due to carbonation. The rate at which carbonation progresses through the depth of the concrete depends on several factors, but notably, a humid environment causes an increased rate of carbonation. In the event that carbonation depth exceeds the concrete cover, the reinforcement loses passive protection. Carbonation is likely to be more advanced in older structures simply due to age. Excessive carbonation is not an issue in dry conditions, but once moisture is present, corrosion can progress at an accelerated rate.
The carbonation depth is typically measured by spraying a phenolphthalein solution onto a freshly cut concrete surface. The solution turns pink in the presence of alkaline conditions (i.e. uncarbonated concrete). For certain concretes, phenolphthalein is ineffective and alternative pH indicators should be used.
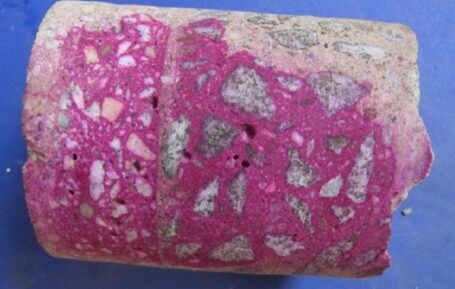
The likelihood and rate of corrosion occurring, is also increased by the presence of chlorides. These can have a major influence on the long-term durability and integrity of concrete structures. Concrete can be exposed to chlorides via several pathways, primarily from external sources like deicing salts, salt water, and marine environments. Corrosion in the presence of chloride can be incredibly destructive and the primary means of mitigation is through design. When specifying the concrete composition, it is normally necessary to adopt concrete with a compressive strength of greater than 40N/mm2. The maximum water content, cement ratio and suitability of additives should also be considered. In existing buildings, it is critically important that concrete containing or exposed to elevated levels of chlorides is kept dry. This is particularly important in historic buildings, where many traditional building materials contain salt from their original manufacture and transportation.
In the late 1940s, following the Second World War, it became increasingly common for the ground floors of buildings to be constructed using ground-bearing concrete slabs, as opposed to imported timber. Due to shortages of construction materials, the government encouraged the use of ‘hardcore’ below-ground-bearing slabs. At the time, hardcore consisted of crushed waste, which included contaminants and deleterious material. These materials often contained sulphate, which attacks chemical compounds that are abundant in the most common type of cement.
It was not until 1965 that the building regulations were updated to prohibit the use of hardcore containing water-soluble sulphates. This reduced the issue but failed to eliminate it completely. The ground on many brownfield sites is contaminated by material containing water-soluble sulphate. These materials can leach sulphate into the ground, creating higher risk conditions for below-ground concrete, such as foundations. Nowadays, sulphate-resistant cements can be specified in place of the more common Ordinary Portland Cement (OPC).
OPC is the most common cement type used in the production of concrete. Other types of cement, or cement substitutes, can be specified to achieve the required concrete characteristics. In the 1950s, High Alumina Cement (HAC) was used in the manufacture of precast concrete elements. It was then banned from use in the 1970s, following several high-profile collapses. Despite this, concrete containing HAC remains in thousands of buildings across the UK. The primary issues affecting HAC concrete are lack of cover, carbonation depth and a chemical process called conversion. Conversion occurs over time and is commonly accompanied by a significant reduction in strength. Investigations have found that the compressive strength of HAC concrete following conversion can be less than 50% of the initial strength.
HAC was typically used to manufacture precast I-beams or X-beams, but it has also been identified in some insitu concrete between 1950-1970. Reinforced Autoclaved Aerated Concrete (RAAC) is composed of two elements: Steel reinforcement (R) and Autoclaved Aerated Concrete (AAC). AAC has existed since the early 1920s and is commonly found in unreinforced blocks for constructing masonry walls. AAC is a precast form of concrete and has several positive characteristics for use in buildings. However, these characteristics are accompanied by low compressive strength and high permeability compared to other forms of concrete. Around 1950, reinforcement was combined with AAC to create precast elements with improved spanning capabilities for use in floors and walls.
There are several issues that affect RAAC including low stiffness and poor detailing of reinforcement, as well as the low strength and high permeability that comes with AAC The durability of RAAC is negatively impacted by the porosity of AAC, which facilitates the penetration of moisture and transportation of harmful chemicals to the embedded reinforcement, increasing the risk of corrosion occurring.
Prevention and Life-Extension
There is little that can be done to rectify reinforced concrete that has been constructed to unsuitable specifications or with poor detailing of reinforcement. However, by identifying potential defects it is possible to avoid conditions that might adversely affect the structure. The issues discussed above are inactive in dry conditions. It is critically important that concrete buildings, new and old, are regularly inspected to identify sources of moisture and changes to the prevailing conditions. Maintenance of the building envelope, supply water, drainage and ventilation systems can help reduce moisture levels and extend the life of concrete buildings. Examples of issues that may adversely affect concrete buildings include:
- Leaking services
- Damaged below-ground drainage
- Water ingress
- Storage of water or chemicals
- Faulty rainwater goods
- Increases in humidity
- Change of use
- Defective waterproofing
Since the characteristics of concrete, and the associated defects, are dependent on several factors, investigations of concrete structures should be undertaken by a competent structural engineer with suitable knowledge and experience of the type of building being inspected.
It is possible to protect concrete structures from deterioration via the introduction of surface coatings and renders or via cathodic protection. These methods are most suitable in scenarios where a concrete structure cannot be isolated from moisture or harmful chemicals. Typical examples include multi-storey car parks, where surface water and de-icing salts are present, or industrial buildings, where processes generate unfavourable conditions. It is fundamentally important that adequate preparatory work is completed to ensure that the remedial measures perform as intended. In the case of cathodic protection, the initial costs can be high, and the system is likely to require ongoing maintenance and inspection.
Summary
The construction industry, like many industries, has often progressed through trial and error. The recent collapses linked to RAAC are one such error that will still be fresh in everyone’s mind, but similar historical issues still affect thousands of buildings. The simplest way to mitigate these issues is through regular inspection and maintenance. Pre-emptive investigations can be conducted to pinpoint potential risk factors, aiding the development of suitable inspection procedures that are tailored to the risks present.
Hawkins’ Built Environment team can assist in the investigation of defects in building structures, whether in a pre or post loss scenario. Our structural and civil engineers can identify factors affecting life expectancy or investigate the cause of failures that have already occurred.
About the Author
Jamie Paterson is a chartered structural engineer (CEng) with the Institution of Structural Engineers (MIStructE) and has a broad range of skills covering onshore and offshore structures. He has undertaken detailed structural investigations of existing buildings, including listed buildings and monuments and has extensive experience of investigating and remediating existing buildings via destructive and non-destructive methods.
Jamie also has experience with modern design methods and low-energy buildings in the context of net zero. In 2022, Jamie became one of the first Passivhaus certified structural engineers in the UK.