WHAT IS A METAL WIRE ROPE?
Metal wire ropes are widely used in hoist (lifting), towing or winching systems, such as cranes and lifts. A metal wire rope is made up of many individual wires that are wound together to form larger elements known as strands. The strands are further twisted into a helix around a central core to form the rope. This design and configuration allows the rope to have good flexibility, as well as to withstand a great deal of engineering stress.
Depending on the requirements, the central core of the rope can be of fibre or metal wire construction; it can also be surrounded by a layer of plastic, which forms a protective cushion between the core and the outer strands, thereby minimising friction. This layer not only enhances the mechanical integrity of the rope, but can also assist in preventing corrosion and wear of the internal core. Furthermore, the properties of the ropes can be altered by changing the lay of the wire rope, or the direction of its twist.

In a rope with regular lay, the wires (forming the strands) are twisted in one direction and the strands are laid up in the opposite direction, which gives an outward appearance that the wires run parallel to the axis of the rope, and provides the rope with greater durability (i.e. less susceptible to crush, untwist and kink).In a rope with Lang’s lay, the wires and the strands are laid up in the same direction, which gives an outward appearance of the wires being diagonal to the axis of the rope, and provides a better resistance to wear during service. Therefore, in an application where the rope is operating over larger number of support rollers and/or sheaves (grooved wheel/pulley), the Lang’s lay rope may be of benefit.
WHY DO METAL WIRE ROPES FAIL?
The most common cause of in-service wire rope failure is misuse, such as over-load or sheave jumping (i.e. the rope jumping out of its groove) caused by inappropriate operation of the winching/hoisting system. However, all wire ropes have a finite life as they inevitably suffer progressive and irreversible degradation in service. Progressive degradation is caused by a number of mechanisms including wear, corrosion and fatigue.
Wire ropes can also sustain damage due to external factors, not related to their operation. These include:
- Lightning strike
- Impact damage from other objects or vehicles
- Thermal damage, possibly caused by either careless welding or metal cutting in the vicinity of the rope
Such types of damage can be very localised. However, even localised damage can seriously compromise the integrity of the rope. If damage goes unreported or unrecognised, rapid, and often catastrophic failure of the rope can result.
HOW TO MINIMISE THE RISK OF FAILURE
To both optimise the life of the rope, and minimise the risk of failure, the rope needs to be carefully selected for its operating environment, as well as maintained appropriately and inspected regularly. A rope should provide safe and trouble-free service if it is: selected correctly, operated and maintained appropriately, inspected regularly, and has not been damaged. A rope must also be withdrawn from service before it becomes degraded to the point where its safety becomes compromised.
In order for the rope to work efficiently as part of a lifting or winching system, it needs to be of the appropriate minimum break strength, as well as of the correct construction and diameter. It must also have appropriate flexibility, which is expressed in terms of its minimum bend radius, to suit the diameter of the sheaves. As a rule of thumb, the greater the diameter of the rope, the greater its minimum bend radius. As such, a larger diameter rope cannot automatically be substituted for a smaller diameter rope, even though it may have a greater break strength, since its minimum bend radius may be greater than the radius of the sheaves over which it is required to operate. That will lead to over-bending of the rope, which will increase the fatigue loading on it, and reduces its service life. Similarly, if the rope diameter is not correctly matched to the sheave groove dimensions, i.e. it is too large or too small, then the load on the rope will be concentrated at certain points on its circumference, rather than being spread evenly. This will also increase the fatigue loading on the rope, resulting in increased wear and subsequently impact its service life.
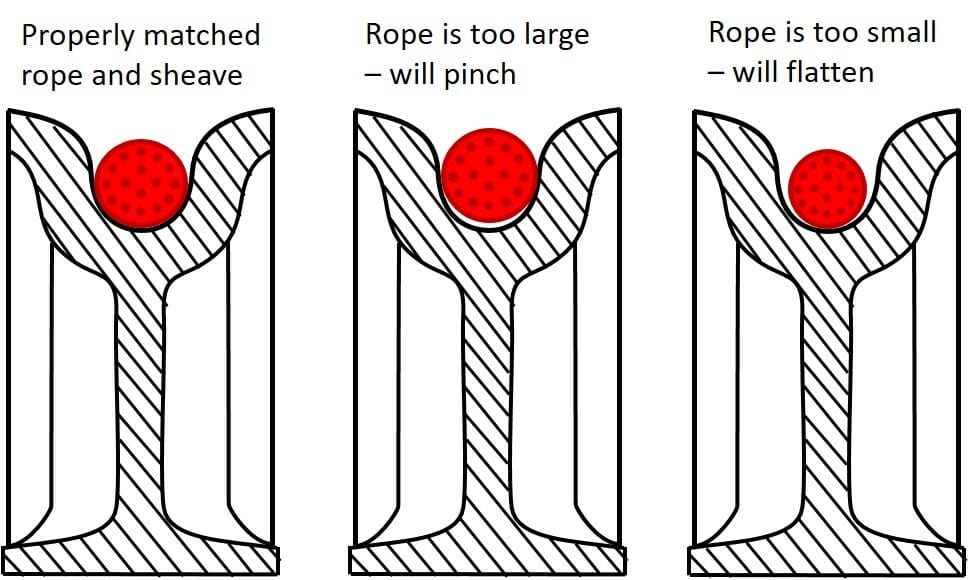
Fatigue causes individual wires to break one by one, usually over an extended period of service, rather than causing a sudden, catastrophic failure of the rope. As the number of broken wire increases, the residual strength of the rope is reduced, so that it will eventually break under normal service loads. In general, the tell-tale signs of fatigue damage are relatively easy to identify; broken wires can often be seen with the naked eye or will protrude from the rope. Fracture surfaces appear straight and perpendicular to the longitudinal axis of the wire. Hence, any rope exhibiting broken or protruding wires should be treated as suspect and removed from service.
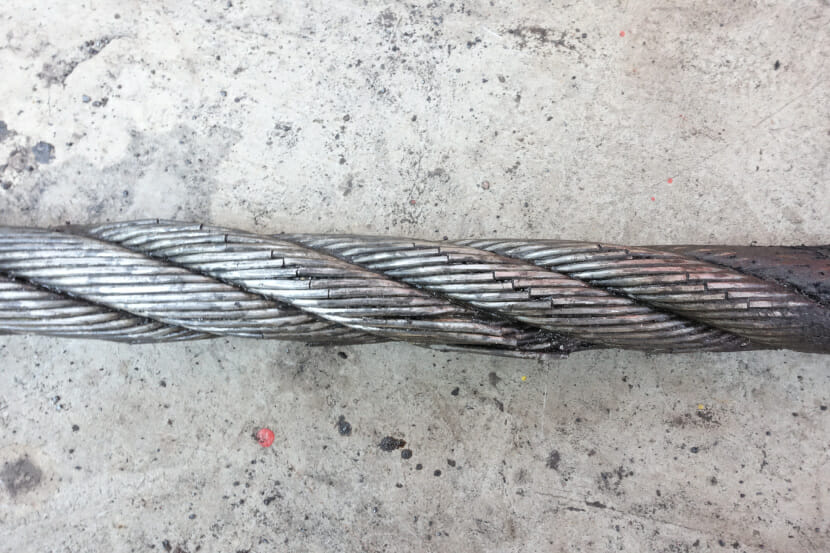
Wear and corrosion are both progressive degradation mechanisms that can be very damaging to metal wire ropes and are often the most life-limiting factors. To reduce corrosion and increase the service life of a rope, in particular when it is used in an outdoor environment, the individual wires within the rope can be protected by galvanisation (zinc coating). Furthermore, wear and corrosion can both be greatly reduced, but not eliminated entirely, by appropriate and regular lubrication of the rope. It is therefore very important that wire ropes are appropriately lubricated (with lubricants such as petrolatum, grease, petroleum-based oils or vegetable-based oils) and checked on a regular basis, particularly where they are operating in arduous conditions, such as a marine environment. This is quite challenging as the method of lubrication must ensure that the interior, as well as the exterior, of the rope is properly lubricated. Simple greasing of the surface is not adequate, and methods such as pressurised grease application need to be used. If it is not done correctly, a rope can sustain significant internal wear, caused by the rubbing together of individual wires as the rope passes over the sheaves and the drums. However, it is also important that the surface of the rope is not covered by an excessive quantity of lubricant, as this could hide and make it more difficult to spot wire breaks during maintenance inspections.
Visual assessment of the rope may indicate damage or degradation, such as wear or corrosion, in the outer layer. However, it will not identify damage or degradation of the internal core. To evaluate the internal condition of the rope, it is necessary to use non-destructive testing techniques. Conventional non-destructive testing method using ultrasound are not compatible with the complex structure of the rope, and more sophisticated methods, such as magnetic flux testing, are required to evaluate the internal condition of a rope. Such testing should form part of a robust maintenance inspection regime for the rope to ensure its safe operation.
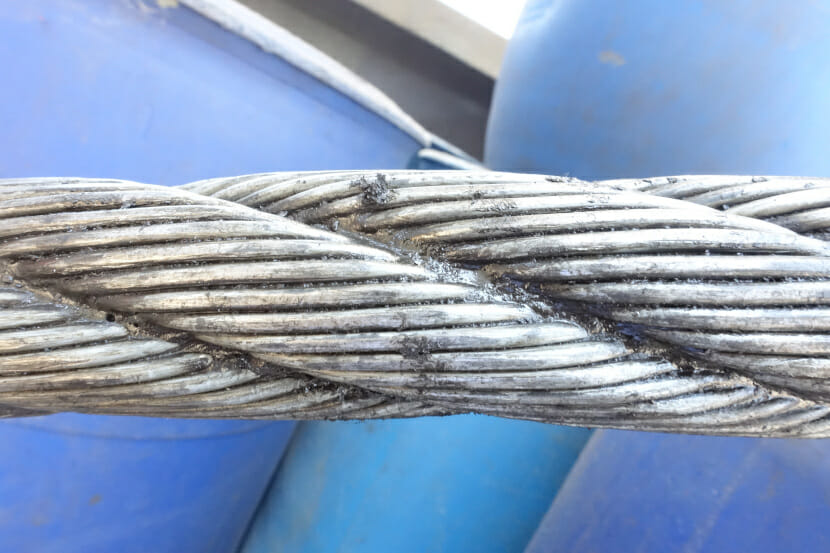
Overall, metal wire ropes remain one of the best options for applications such as lifting/hoisting and the transmission of mechanical power. Compared to their counterparts, such as chains and fibre ropes, metal wire ropes have a high strength combined with a good strength to weight ratio, which make them easier to handle/install for heavy duty tasks.