Age might just be a number, but in the world of plant management, that number can weigh heavily on operation and production. An ageing plant portfolio may remain at the forefront of the production race but can often require a metaphorical knee brace and the occasional pep talk, whilst younger, ‘infant’ plants face their own teething troubles, but that’s a story for another day!
Operating like tireless workhorses, running nearly 24/7, all year-round, with only brief, often obligatory turnarounds for planned overhauls, ageing plants can become increasingly vulnerable to unplanned shutdowns. Such interruptions can lead to costly business disruptions, urgent equipment rentals, and potential public or environmental consequences. Unplanned shutdowns arise from both foreseeable and unforeseeable factors. While some incidents (such as vandalism, power outages or natural disasters) are beyond our control, a deep understanding of a plant’s operational and environmental risks can help mitigate predictable issues.
The Usual Suspects: Material and Mechanical Damages
Degradation Due to Processes
Material degradation, including corrosion, cracking, and erosion, is inevitable over time. It’s not a question of if, but when. Whether localised or uniform, this creates weak points that reduce the structural integrity of equipment. These can range from hairline cracks to tower collapses.
There are various types of documented process-induced corrosion and cracking mechanisms, including stress corrosion cracking, hydrogen-assisted cracking, acid and alkaline corrosion, dead-leg corrosion, and mix-point corrosion. Erosion, on the other hand, is often the result of flow dynamics.
Identifying potential vulnerabilities through process data and analysing inspection records allows for timely repairs or replacements, minimising the risks posed by such degradation.
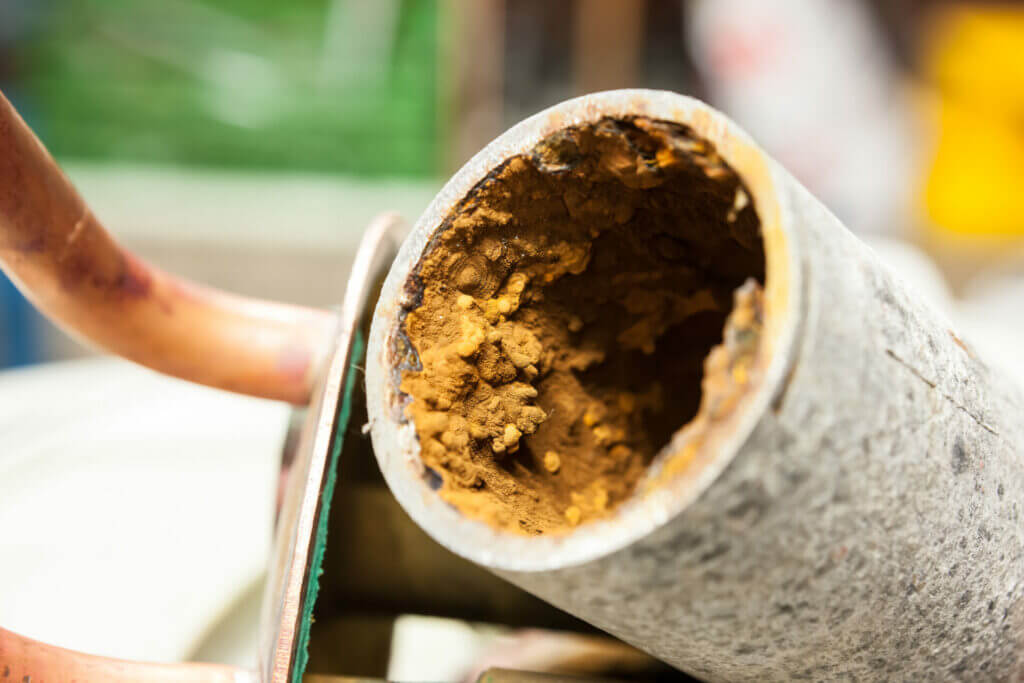
Degradation Introduced or Accelerated by Changes
Both expected and unexpected changes can significantly affect equipment. Over time, repetitive stresses from temperature and pressure fluctuations, as well as process variations, can create or exacerbate faults and cracks, often without warning. Hence, the inclusion of cyclic degradation factors is crucial in equipment risk assessments.
Abnormal, one-off events, such as backflow, carryover, or contamination can introduce sudden stresses. If not addressed, these can lead to catastrophic failures. Detecting abnormalities and conducting thorough inspections of all susceptible areas before restarting operations is critical.
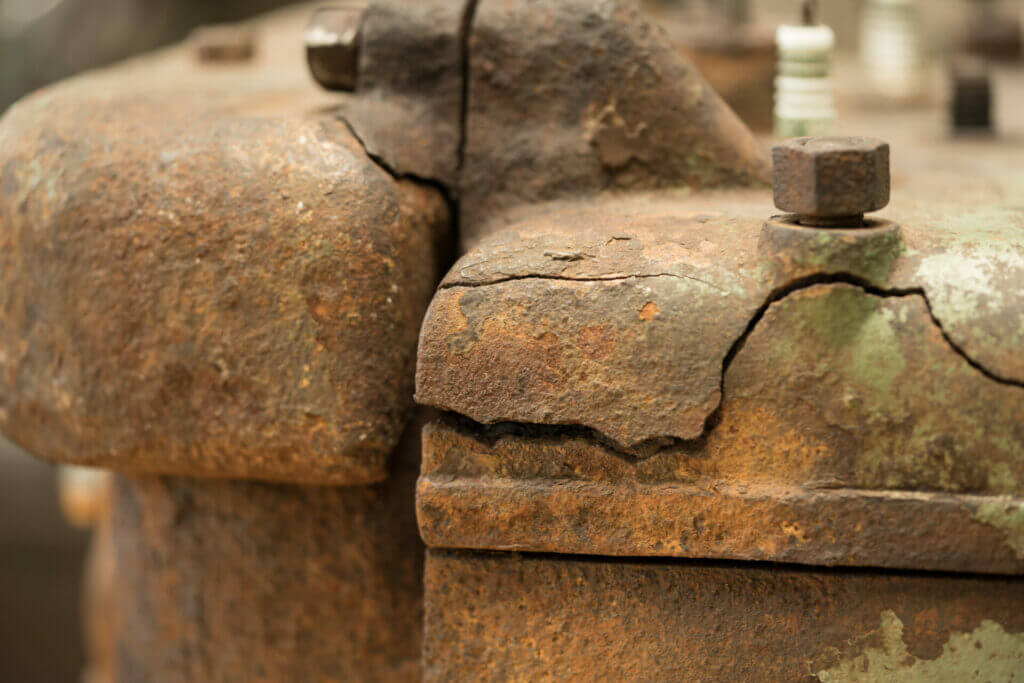
Degradation Due to Environmental Factors
The environment surrounding equipment can be just as damaging as the internal processes. Chloride-laden air, steam leaks, and extreme weather patterns wreak havoc on ageing equipment. Low-impact leaks, such as those involving steam, firewater, air, or nitrogen, may seem harmless but can corrode adjacent equipment, potentially causing more severe issues.
Incorporating comprehensive event tree analysis into risk assessments (or at least during maintenance planning) can help identify and address these hidden threats.
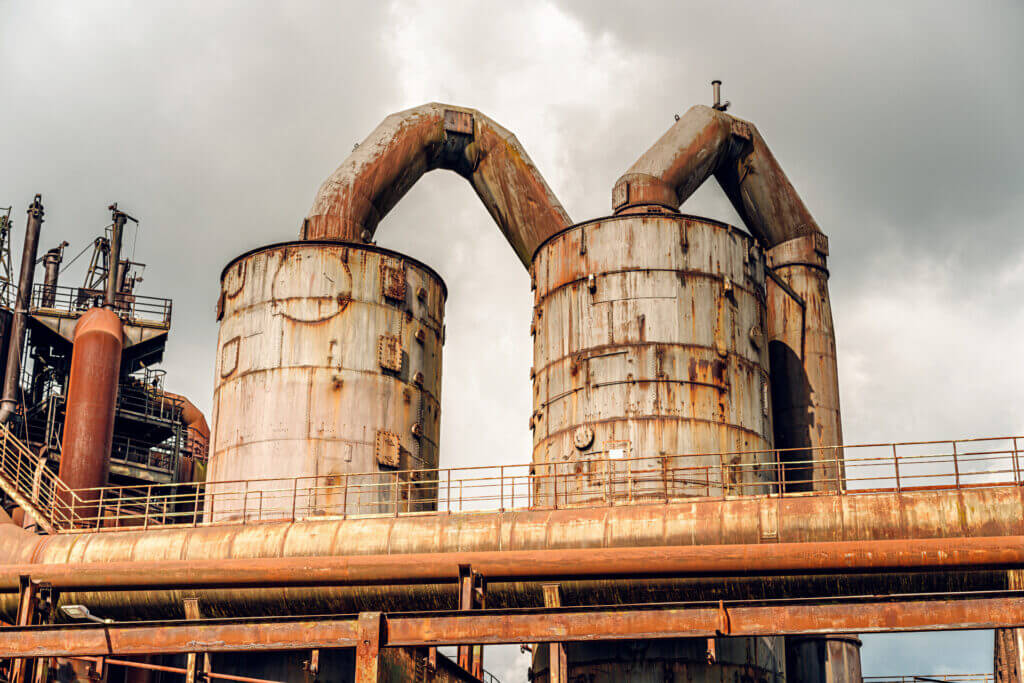
Mechanical Damage
Mechanical degradation arises from a range of factors, including vibration, inadequate design, and human error. Ageing plants are particularly susceptible to time-dependent stresses. For example, poorly designed pipe supports or insufficient allowances for thermal expansion in pressure vessels can lead to significant failures over time.
A walk through an ageing facility might reveal makeshift solutions – pipes precariously secured with ropes, bricks used to prop up supports, or tape hastily covering leaks. While these ‘creative engineering’ fixes may temporarily keep operations running, they often signal deeper systemic problems, such as outdated designs or deferred maintenance. Addressing these issues with properly engineered supports, adequate thermal allowances, and comprehensive stress analyses is not a luxury, it’s a necessity.
Furthermore, mechanical damage such as impact damage can result from improper equipment handling, such as forklift collisions, or seemingly minor actions like walking on pipes during inspections, causing cumulative damage over time. These incidents underscore the importance of rigorous training programmes and robust operational processes to minimise risks and extend the lifespan of critical equipment.
The Curse of Poor Documentation
One of the most significant challenges in ageing plants is the loss of historical data. Over the years, critical documents, inspection reports, failure records, and operational guidelines often disappear. Coupled with workforce turnover, retirements, or inadequate knowledge transfer, this creates ample room for operational errors. In the digital age, robust documentation is both proactive and prudent. Key areas to focus on include best practices to avoid failure, identification of bad actors (components or systems prone to failure), and historical process or design changes. Knowledge management is not merely about retention, it is vital for survival.
Prevention Is Better Than Cure
While ageing plant will never operate like new, strategic planning and risk management can ensure they run safely and profitably.
Essential measures that can be taken include:
- Data-driven decisions - Use inspection data to predict long-term degradation trends and schedule maintenance proactively.
- Regular training - Equip new operators with a thorough understanding of both historical and current best practices.
- Proactive monitoring - Invest in condition-monitoring technologies to detect abnormalities early.
- Design reviews - Address engineering inadequacies, such as insufficient equipment supports.
- Environmental mitigation - Manage external risks, such as chloride exposure or extreme weather, through protective coatings, barriers, and timely maintenance.
Conclusion: Aged but Not Out
Even though ageing plants present unique challenges, they are far from obsolete. By understanding common damage mechanisms, prioritising preventative measures, and maintaining meticulous records, operators can extend the life of these facilities. A well-maintained ageing plant is more than a relic of the past, it’s a testament to resilient engineering. If your plant is starting to feel the creaks of ‘plant arthritis,’ Hawkins can help investigate, mitigate, and future-proof your operations.
About the Author
Divyeruthra Muniandy is a mechanical engineer at Hawkins, with experience in root cause analysis and risk assessment for refineries and petrochemical plants. She specialises in failure investigations for the insurance and legal sectors, with expertise in process degradation, mechanical and material failures, contamination, business interruption, fire, explosion and marine losses.