Product designers are often faced with complex requirements when considering how to join components together, such as aesthetics, weight saving or part-count reduction. Adhesive technologies provide a compelling solution, especially in cases where traditional mechanical fasteners (e.g. rivets or screws) are less suitable. Unfortunately, confidence in adhesive technologies can often be low, particularly in cases where joint failure could cause damage or injury.
At some point, most engineers have observed a failed adhesive joint; for example, when an adhesive has been used to repair a damaged product, only to fail again shortly after. This often results in a cautious approach to adopting adhesive technologies. Failure can often be attributed to one of a few common root causes. With a thorough approach to joint design, and validation at the design stage, much greater reliability and confidence in the final joint can be achieved. This article covers some of the more common causes of adhesive failure and provides suggestions to help ensure a reliable solution.
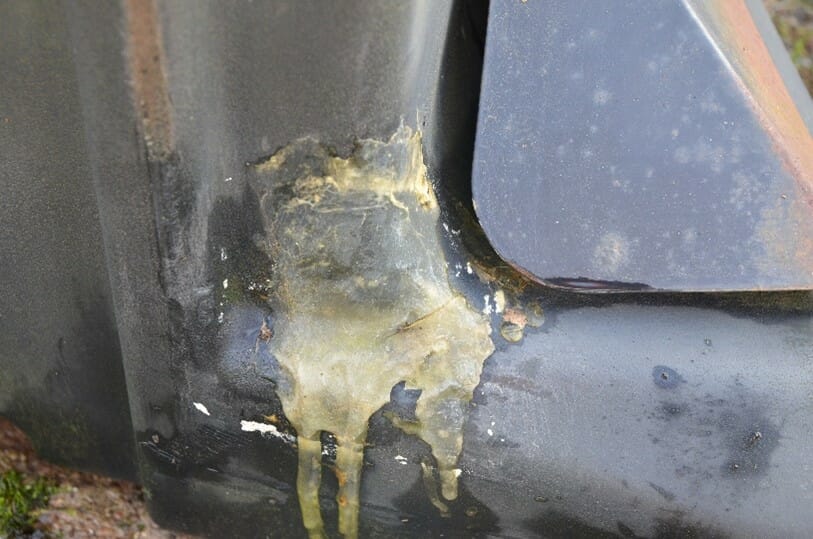
Designing for the use of adhesives from the outset can have a big influence on the ultimate lifespan of the joint. Adhesive joints are inherently vulnerable when subjected to peel loads: think of removing a plaster. For cleavage loads, think of trying to separate frozen food.
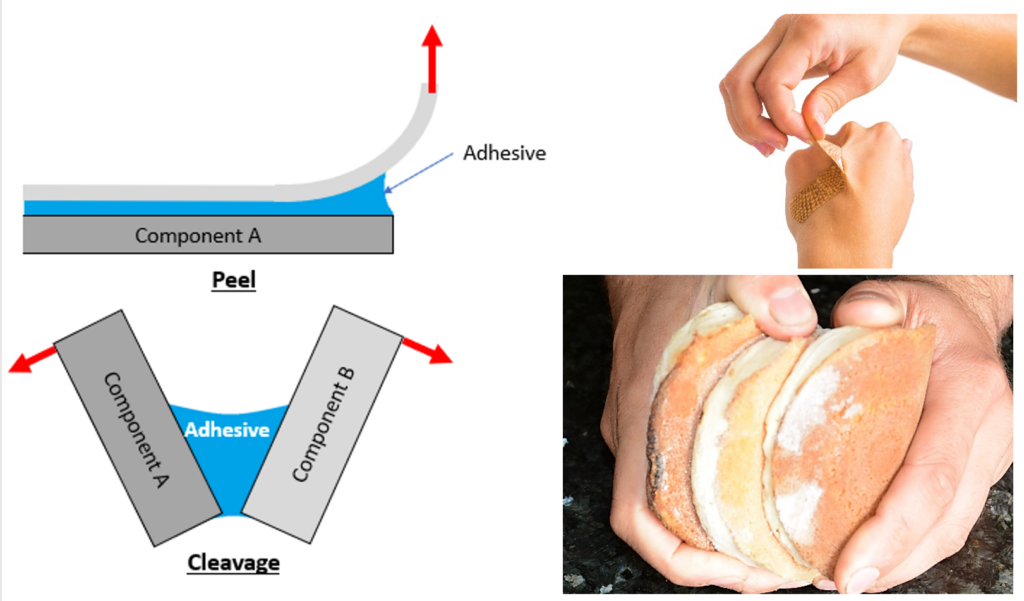
However, adhesives can excel when loaded in shear, such as when trying to unscrew the lid on a previously used bottle of sticky liquid. They also perform well in compression or tension, in this case think of trying to pull apart soft sweets! Where possible, an adhesive joint should be designed to avoid peel or cleavage loads.
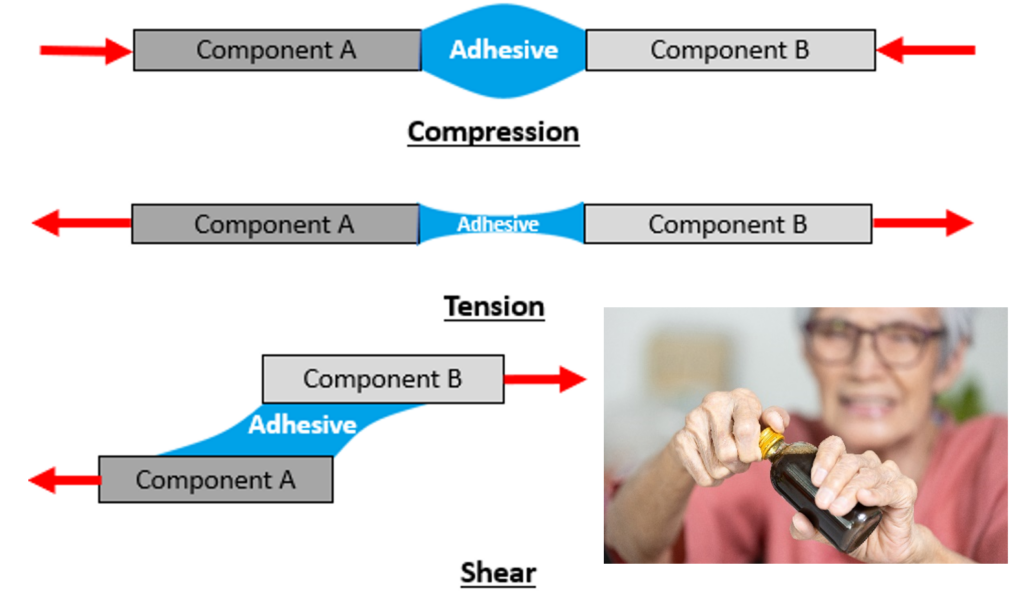
From the outset, it is important to identify a suitable adhesive for the application, which can be challenging without specialist advice. Whilst adhesive manufacturers generally have representatives willing to support joint applications, it is important to share as much information about the application as possible. Failure to do so could result in recommendations being unfit for purpose. For example, failing to mention that the service temperature for an application may exceed the norm, even for short periods of time, could result in premature failure.
When selecting an adhesive, the materials to join (often referred to as substrates or adherends) are also an important consideration. Certain adhesive chemistries are inherently more or less suited to different material combinations. Certain thermoplastics, for example polypropylene, are notoriously difficult to bond, and specialist adhesive products exist for such materials. This is where the advice of a product specialist can be used to great effect. Similarly, the selected adhesive must be able to accommodate any flexibility in the substrates. Selecting an adhesive which is too stiff for flexible substrates may well result in premature failure, particularly if thermal expansion needs to be considered.
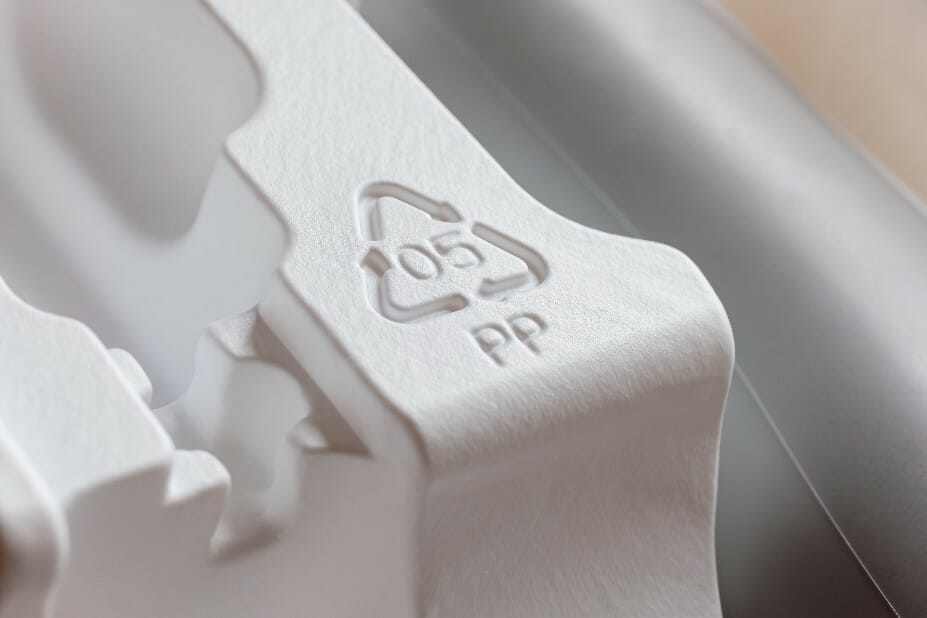
If the strength required from an adhesive is relatively modest, pressure sensitive tapes may provide an attractive alternative to traditional paste type adhesives and often work well with difficult to bond materials. Modern high-strength bonding tapes are increasingly moving into the semi-structural realms of adhesive bonding. These tapes can achieve high strength bonds when applied appropriately, often with minimal surface preparation even on difficult to bond materials.
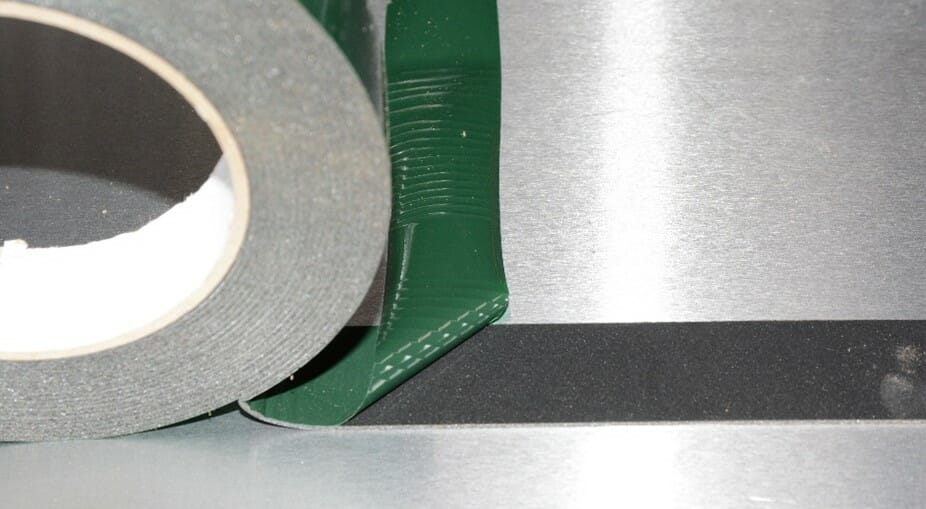
Inevitably, it will be necessary to calculate the required joint overlap for a given joint design. Simple hand calculations are a great starting point, based on both the expected forces involved and the expected strength of each possible adhesive from the product data sheets. However, stress concentrations at the edges of joints can initiate failure at a much lower load than might be expected. This effect increases with the stiffness of the adhesive. A smooth transition at the edge of the joint, known as a fillet, can help to reduce this problem, as can more flexible adhesives and increased factors of safety.
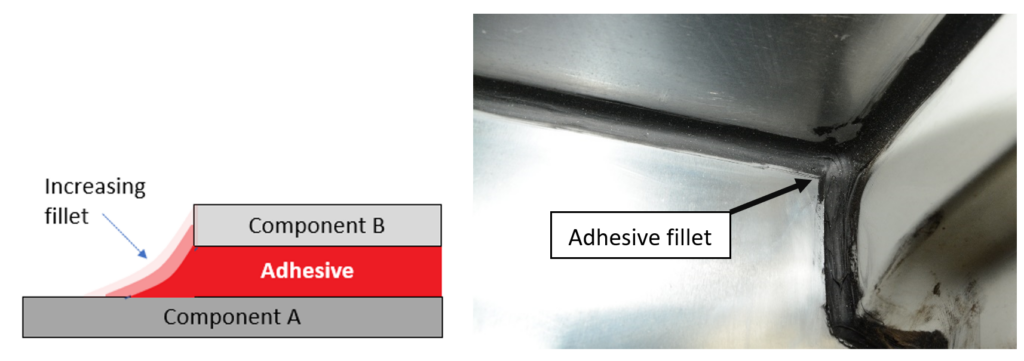
Often prototype components may use different manufacturing methods, or even different materials to their production counterpart. This can result in a surface that is fundamentally different to that in production. Unsurprisingly, adhesive bonding results generated with the prototype components can differ to those achieved with the final product. It is advisable to conduct product compatibility tests at an early stage, and to keep the materials representative of those used in final production.
Effective surface treatment, prior to adhesive bonding, is often a critical step in achieving a reliable joint. Though this step is often overlooked, it can both remove contamination, which may act as a barrier to adhesion, as well as improve the compatibility of the adhesive with the surface. A solvent wipe is a simpler way to treat a surface. Moving further up the complexity scale is abrasion, which can be effective with some materials, followed by a solvent wipe to remove any loose debris. The most complex types of surface treatment are specialist primers and methods, such as plasma or flame treatment. When used appropriately, these methods can significantly increase both bond strength and joint durability. Many surface treatments become less effective as time elapses between the treatment and application of the adhesive, which is also important to bear in mind.
Whilst many adhesives may perform well at ambient temperature in the lab, their results may also be very different at elevated temperatures. Likewise, wet environments can push joints to failure, particularly when combined with elevated temperatures. Helpfully, many well-established standards exist for durability testing; albeit the designer must ensure these are relevant to the service environment. Conducting additional durability testing, under environments that closely replicate those from the joint in service, may be necessary to ensure the required performance is achieved.
Predicting performance over a long service life, during a much shorter product development cycle, is a long-established problem for the adhesives industry. Be conscious that “turning up” the parameters in the durability test, won’t necessarily produce useful results. For example, testing at an increased temperature in a humidity chamber won’t necessarily enable the results to be extrapolated over longer time periods at lower temperatures. Depending on either the required confidence in the joint or complexity of the service environment, conducting different environmental tests may be necessary. Varied tests will develop a product designer’s confidence in the joint to outlive its projected service life. Product suppliers, and/or independent specialists may be able to assist with such tests.
In a previous investigation, the failure of an adhesive joint occurred, resulting in the total detachment of a component at high speed. The bonding process was well established, and this was the first reported failure in the field. After a detailed inspection and analysis, it was determined that during a recent re‑configuration of the manufacturing process, part of the adhesive primer system had been omitted. It was found through subsequent testing that this omission significantly worsened the joints long term environmental durability. This eventually resulted in a failure of the adhesive joint, after long term exposure to a specific combination of environmental conditions.
Whilst there are many more factors to consider, which have not been covered in this brief article, early consideration of the above points should reduce the likelihood of premature adhesive joint failure.
If you are dealing with the failure of a component or a structure made from a composite material, and you want to know what has caused it and how to prevent the same thing from happening again in the future, you need a forensic investigator.
At Hawkins, our investigators have an in-depth knowledge of the regulations, guidance and best practices that should be followed during manufacture, assembly and/or installation of a composite part. Experts in their field, they are knowledgeable in a wide range of areas and can investigate all aspects of composite material’s failure.
We can provide you with an expert who is familiar with all aspects of a case and can offer clarity and answers to your questions.
ABOUT THE AUTHOR
Richard Woodward completed his Engineering Doctorate in 2017 at The University of Warwick, focused on the development of adhesive bonding technologies for the high-volume manufacture of fibre-reinforced composite intensive vehicles. Prior to joining Hawkins, he has worked within the automotive industry in the field of adhesive research and development.