Hydrogen, from its explosive potential to its benign, life giving properties after reacting with oxygen, is one of the most dynamic elements.
A lesser-known phenomenon is hydrogen’s ability to embrittle certain metals. Typically, when we think of the properties of metals, their ability to bend and stretch (often substantially) before they break is one thing that comes to mind; this is termed ‘ductility’. More formally, tensile ductility is the amount of deformation a material undergoes before fracture occurs when the item is pulled to failure. Deforming prior to failure is nearly always a good feature, because it can warn people of an impending catastrophic failure.
Hydrogen embrittlement causes some metals to lose their ductility, become brittle, and fracture, and is a well-documented occurrence that can result in the apparent sudden failure of a component.
Hydrogen embrittlement and Hydrogen Induced Cracking (HIC) are two of several documented mechanisms by which hydrogen can damage materials. HIC, closely related to hydrogen embrittlement, is hydrogen damage that produces flaking and blistering of materials.
A stress is required for an item to fail by hydrogen embrittlement. The stress can either be applied or residual. An example of applied stress would be the tensile stress on a bolt, when used to clamp two plates together in service, or the tension in a wire from which a weight is hung. Residual stress can come from rapid cooling during heat treatment, welding, or deformation, as well as from manufacture and processing.
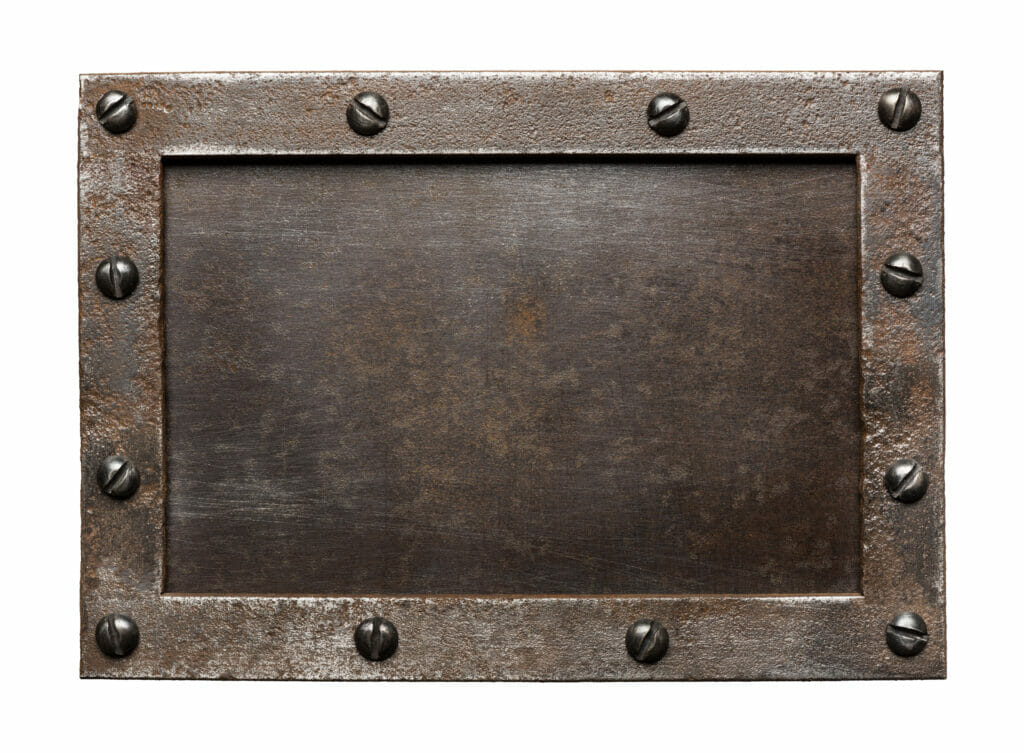
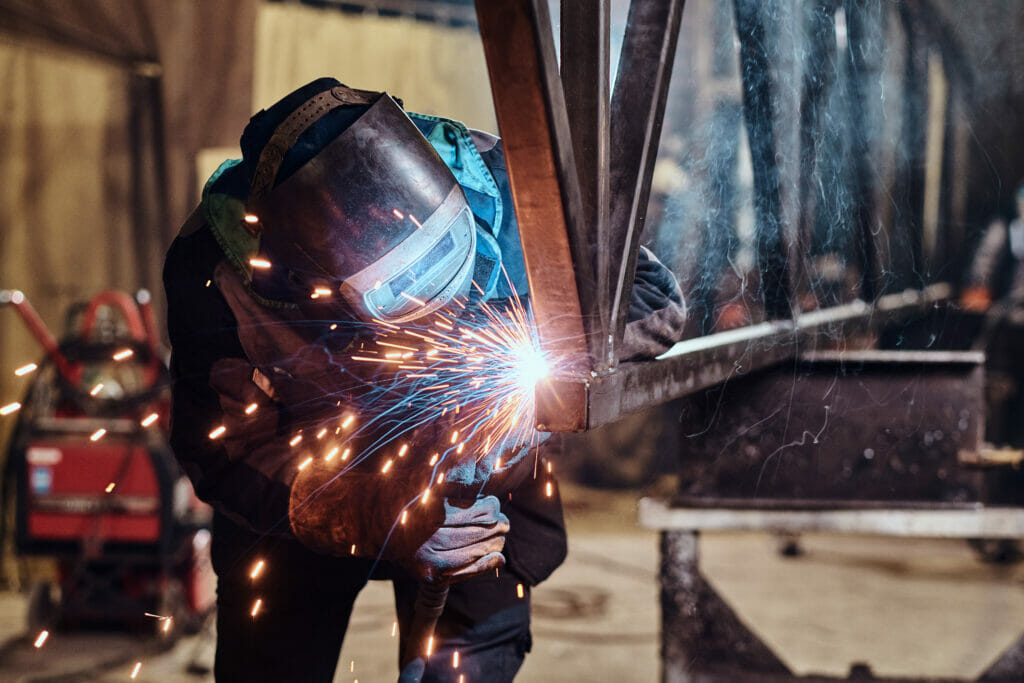
Tensile stress -v- Residual stress on metals
A frequent feature with hydrogen embrittlement is a delay between a component’s seemingly successfully initial service life (e.g. tightening of the bolts to the required torque during assembly did not result in them breaking) and its subsequent sudden failure (fracture of the threaded bolt shaft, some hours, days or weeks after it was installed).
I have known of assembled items, whilst awaiting shipment at a port to their final customer, to be brought back to the manufacturing facility, because sample testing of the same production batch of bolts over several days had found the bolts to crack due to hydrogen embrittlement.
Hydrogen is ubiquitous in the environment, as well as in many manufacturing environments. Common sources of hydrogen are:
- Melting of the metal (including welding)
- Treatment of the metal surface (pickling, electroplating)
- The service environment (the degradation of materials and corrosion in certain cases)
Nascent hydrogen (atomic hydrogen as opposed to the usual molecular H2 it forms) can be produced by those processes. Nascent hydrogen can be readily adsorbed into a metal’s structure, and once in that structure it can move/diffuse very rapidly. Precisely how hydrogen causes embrittlement is still debated. A few parts per million (i.e. a few 0.0001%) can be enough hydrogen to induce a failure where sufficient stress is present.
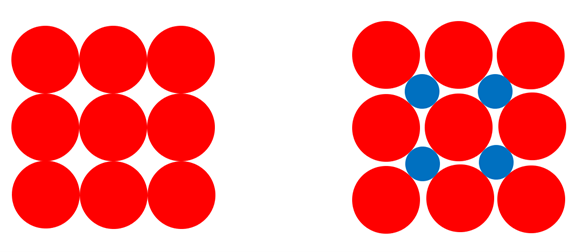
The atoms in metals predominantly form an ordered structure, a bit like oranges stacked for display. In the above illustration, the red circles represent the atoms of the metal in a crystal structure (the lattice) and the blue circles represent hydrogen that has dissolved (diffused) into the metal. The hydrogen fills the space between the metal atoms and in doing so forces the metal atoms apart slightly.
Classification
Three classifications of hydrogen embrittlement are commonly used:
- Internal reversible hydrogen embrittlement
- Hydrogen environment embrittlement
- Hydrogen reaction embrittlement
The first of those, internal reversible hydrogen embrittlement, is often encountered at moderate temperatures (i.e. below 100°C). It is most common in high strength steels and steels that are heavily deformed (cold worked). Other commonly encountered metals which are at notable risk, are nickel alloys and austenitic stainless steels. In lower strength steels, a loss of tensile ductility occurs. For a susceptible material, where sufficient hydrogen is present and the rate of deformation is sufficiently slow, then marked reductions in elongation happen before the material fractures.
Hydrogen stress cracking occurs even where no external tensile stress is present. It is often associated with cold work and stress raising features.
To the engineer, the good news is that internal reversible type of hydrogen embrittlement, as the name suggests, is largely reversible. Moreover, the process can be controlled to reduce the risk of it occurring. Process controls can include either monitoring of plating bath chemistry or baking of welding rods to drive off water before they are used. Typically, components can be baked (heated at about 200°C, for steel, in an oven for nearly a day) before being put into service. As the solubility of hydrogen in a metal reduces with increasing temperature, the baking process will reduce the amount of absorbed hydrogen, so reducing the susceptibility of an item to hydrogen embrittlement. Often the effectiveness of either baking or process control is determined by the use of test pieces, upon which a static load (weight) is placed. The weight is selected so that it provides a defined percentage of the strength of the item (e.g. a bolt might be loaded to 75% of its yield strength and the weight left suspending for a set period of time) and there are other more involved approaches to this as well.
The delay to failure from hydrogen embrittlement can result in very difficult situations as materials may be quality checked and approved for despatch and subsequently fail at a later date. For example: the packing case of an assembled piece of machinery is found to have several fractured bolt heads on the floor after the packing case was opened during shipping, or test pieces fail after 48 hours on test, where the equipment has already been shipped to the customer.
As noted above, the in-service environment can cause hydrogen to adsorb at the surface of the metal, and then diffuse into the metal, which results in damage. Adsorption is different from absorption in that the chemical clings on the surface of a molecule like a film, rather than entering it. An often-cited example of this is the cracking of high tensile steel in both fresh or marine waters.
When either applied or residual stresses are sufficiently high in steels with tensile strengths generally greater than 1200 MPa (Megapascals), then delayed cracking due to hydrogen adsorption into the steel during corrosion can occur. 1200 MPa roughly relates to the stress in a 1.1 mm thick wire with a weight of 12,236 kg hanging from it (about the weight of a double decker bus). At that load, the wire with a tensile strength of 1200 MPa would fail.
Sour environments (where hydrogen sulphide is present), such as those encountered in the oil and gas and processing industries, can also result in hydrogen being adsorbed into the metal; in this case, it can also be referred to as sulphide stress cracking.
Hydrogen reaction embrittlement, and associated cracking, occurs when hydrogen forms chemical bonds with the material. Many metals form hydrides, and those compounds tend to be brittle, promoting cracking at lower stresses than expected. Metal hydrides can be used for hydrogen storage.
Characterisation
Characterisation of hydrogen embrittlement is not simple, as it can have features similar to other failure mechanisms. The failure region typically shows either limited or no apparent macro scale deformation prior to failure. A delay is often present between the applied stress occurring and the fracture’s occurrence. Fracture typically initiates either at the surface or near to the surface. However, the fracture’s form can be either transgranular or intergranular (i.e. either through or around the microscopic crystals that form common engineering metals). In addition, the fracture surfaces might show:
- Brittle cleavage—no apparent deformation before fracture even at the microscopic level)
- Quasi-cleavage—no general deformation prior to failure unless inspected at very high magnification (such as by using a scanning electron microscope)
- Micro-void coalescence—the ductile mode of failure, but this is typically confined to a few isolated regions or a ‘final failure’ region.
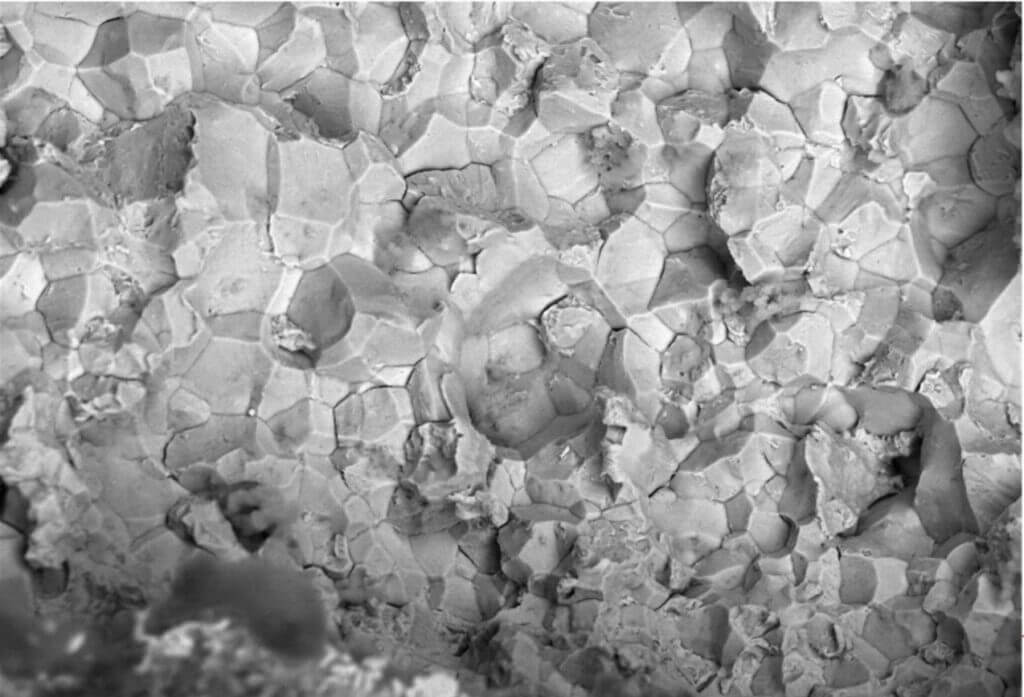
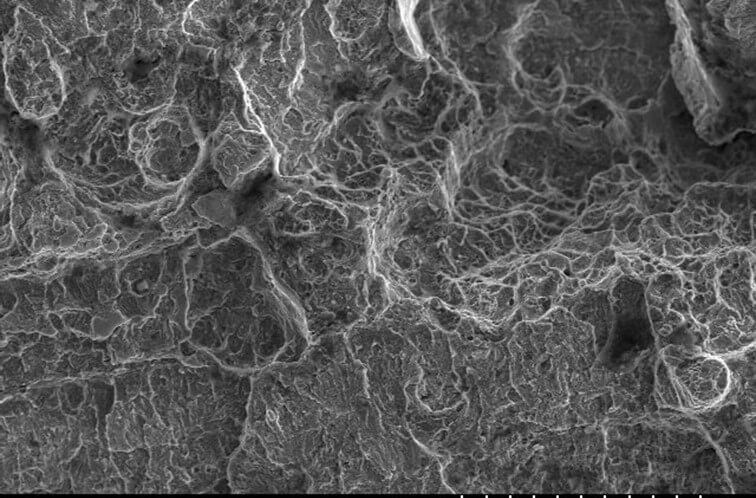
Furthermore, a failed component might show several, or a mixture of those features, over the fracture surface as the crack has grown (propagated) through the material. This seemingly contradictory morphology (surface shapes) varies due to the strain rate, stress state, material, and microstructure, amongst other factors. Hence, a detailed examination is required to confirm the exact mechanism of hydrogen embrittlement.
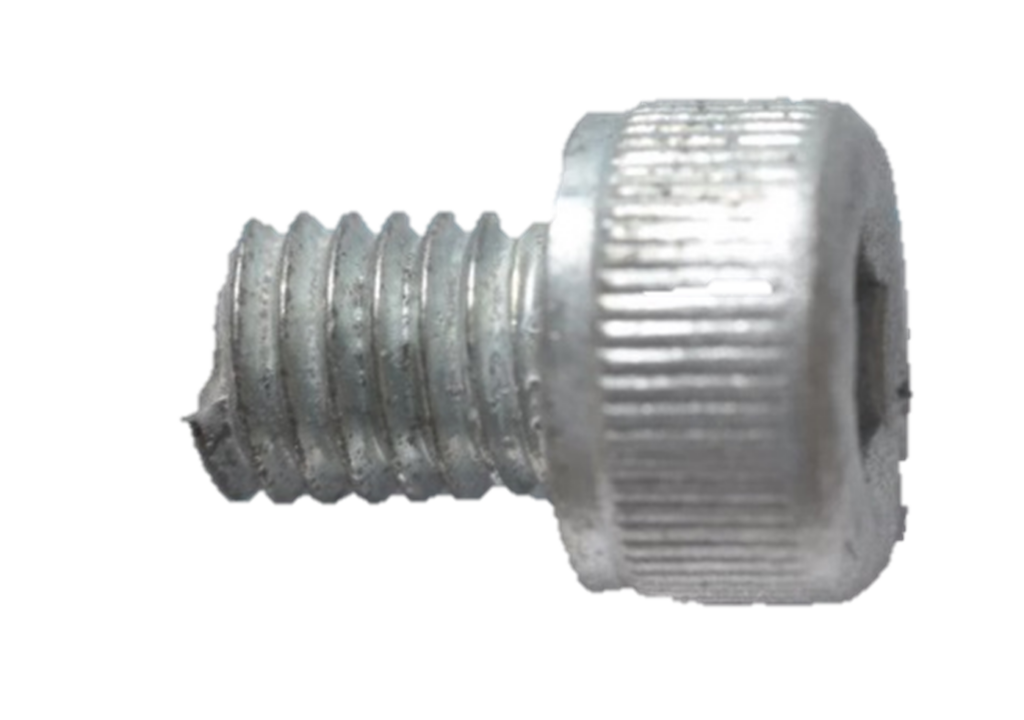
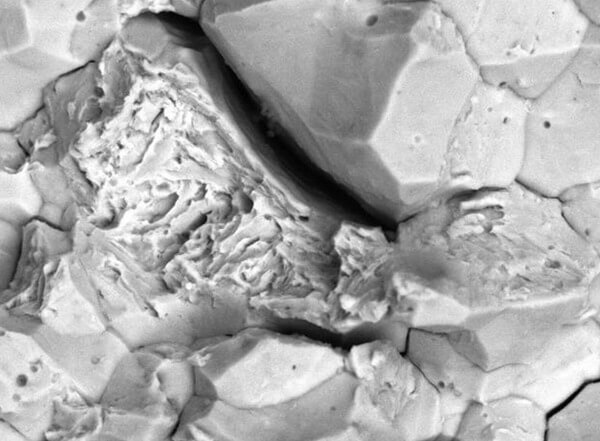
In summary, many of the causes of hydrogen embrittlement can be related to either poor manufacture or design and to understand the root cause of a failure, a careful and detailed analysis is required.
ABOUT THE AUTHOR
Neville Tranter has undertaken failure analysis, with specific interest in investigating materials failures, since 2005. During that time, he has reported on numerous failure mechanisms, including hydrogen embrittlement. He has worked in aerospace, where control of processes to reduce the impact of hydrogen was an essential production aspect.
During his tenure at Hawkins, Neville has investigated over 100 metallurgical and failure investigations including:
• multi-million pound oil and gas industry losses
• medical devices and equipment
• railway rolling-stock and systems
• consumer products and patent infringement.
If you would like Neville, or a Hawkins expert from any other discipline, to investigate a case or present to your organisation, please contact us and we will be happy to discuss the range of services that we can offer.