In the period between 2017 and 2018, the Health and Safety Executive (HSE) reported a total of 144 fatal injuries, and 71,062 non-fatal injuries, in the workplace under the RIDDOR procedure. The Reporting of Injuries, Diseases and Dangerous Occurrences Regulations requires both employers, and managers of certain premises, to report work-related accidents and deaths to the relevant authority. According to the HSE, the estimated cost of these workplace injuries was in the region of £5.2 billion.
Of the fatal injuries, 35 were attributed to falls from height, and 23 were attributed to strikes by moving objects (including flying/falling objects), accounting for approximately 40% of the cases reported. For the non-fatal injuries, those numbers are 5,445 and 7,024, respectively, accounting for approximately 17.5% of all reported cases.
Many of these cases were due to the fact that there were either people or objects at height when something went wrong. According to the Management of Health and Safety at Work Regulations 1999, it is the legal responsibility of an employer to minimise and eliminate as much ‘work at height’ as possible. This is done via implementing the ‘hierarchy of controls’, where putting people at height should be a last resort, as outlined in The Work at Height Regulations 2005.
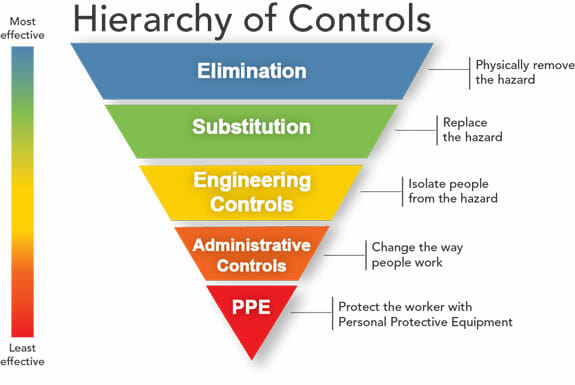
Lifting operations should be eliminated as far as reasonably practicable, but are unavoidable in many circumstances. There is abundant UK legislation that must be complied with for lifting operations, but the main governing document for these operations is the Lifting Operations and Lifting Equipment Regulations 1998 (LOLER). The main part of LOLER is Regulation 8, “Organising of lifting operations” which gives three main requirements for lifting operations:
“Every employer shall ensure that every lifting operation involving lifting equipment is –
- Properly planned by a competent person;
- Appropriately supervised; and
- Carried out in a safe manner.”
The first requirement is to produce a Lifting Plan. In simple terms, the purpose of a Lifting Plan is to ensure that any lift is properly understood, fully controlled, and executed in a safe manner. Mr Richard Giles-Carlsson, of Hawkins’ Manchester Office, explains the full meaning and purpose of the Lifting Plan in an article that is available on the website here.
The purpose of this article will be to take a more focused look at the selection of the appropriate equipment for the lifting operations.
There is a wide range of legislative documents that cover the equipment for lifting operations, the main documents being:
- Lifting Operations and Lifting Equipment Regulations 1998 (LOLER)
- The Provision and Use of Work Equipment Regulations 1998 (PUWER), aimed generally at the employers and users of the equipment
- Supply of Machinery (Safety) Regulations 2008, aimed generally at manufactures and suppliers of equipment
The specifics of the equipment may be different, depending on whether the equipment is used as personal protective equipment (PPE), when a person is operating at height, or on whether it is used as lifting equipment, when a person is being lifted as a ‘load’.
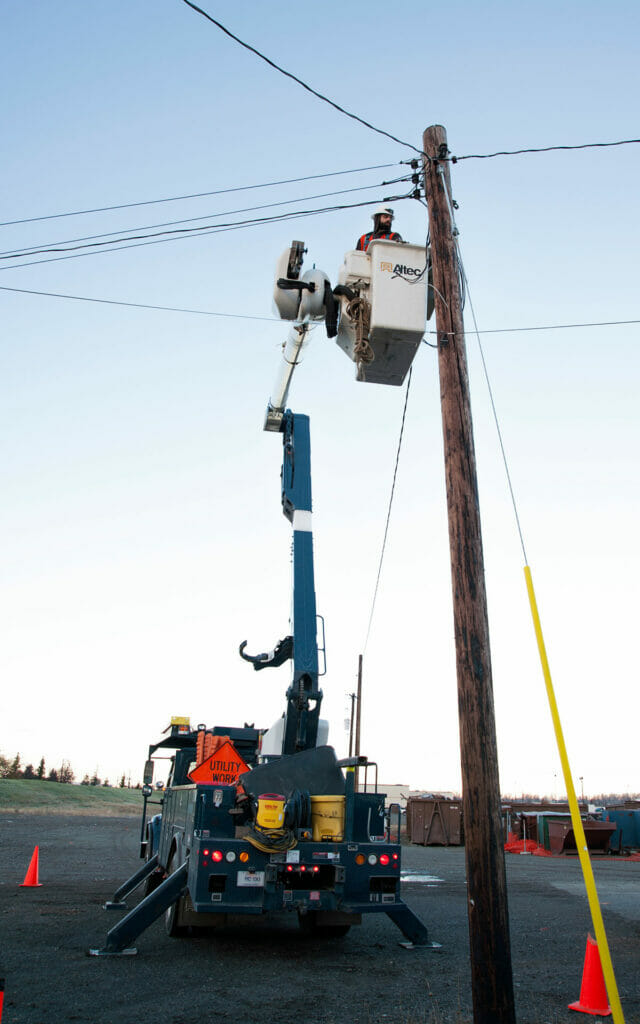
There are three main types of lifting sling: synthetic fibre, chain, and wire rope. This article will consider both the use and failure of synthetic fibre lifting slings. The exact numbers are not available, but nearly 100% of failures of synthetic fibre slings are due to improper use, rather than manufacturing defects.
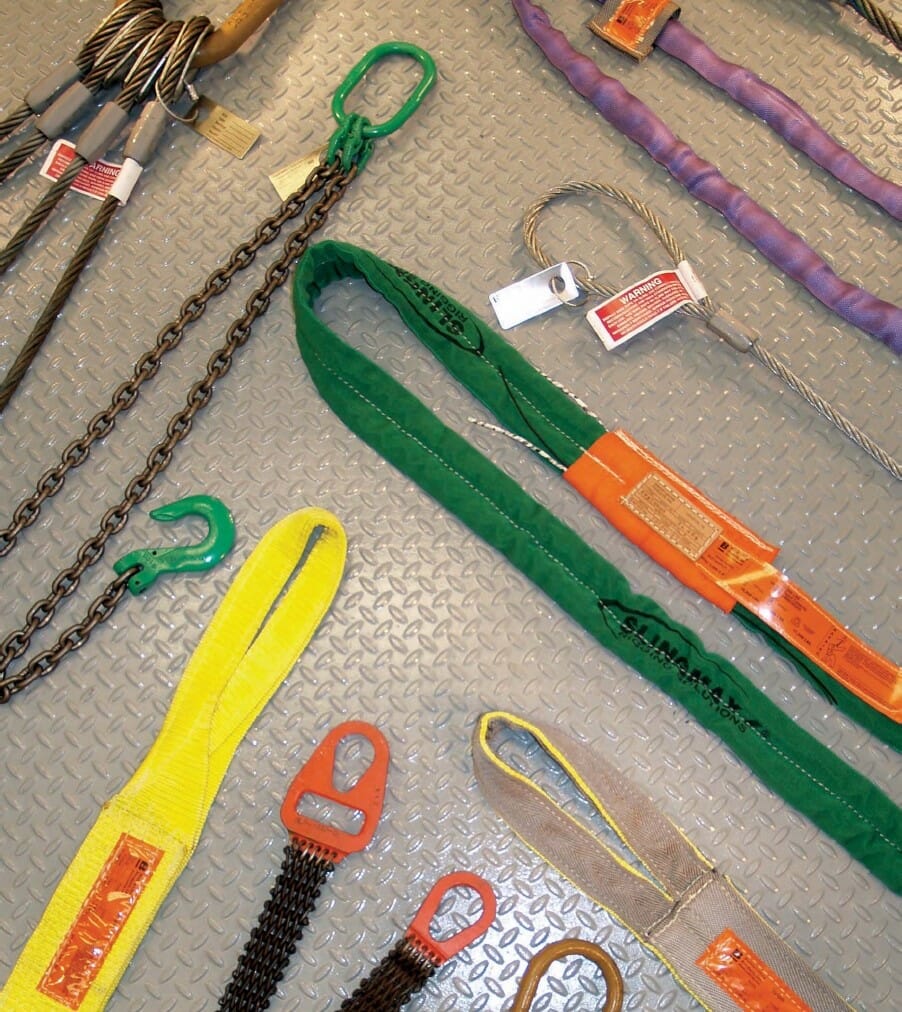
Synthetic fibre slings can be made from various materials, including polyester (PE), polyamide (PA), and polypropylene (PP). Slings made of these materials can be individually rated between 500 kg and 450 tonnes in a straight lift. Many people do not like to find out that these slings are technically only held together with a small amount of tape.
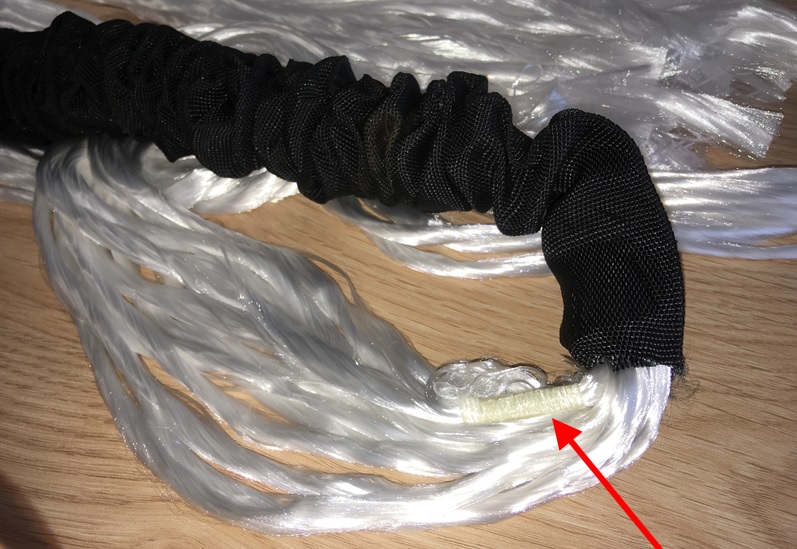
What gives these slings their strength is the friction between the many individual yarns wrapped in a circle. These slings are also manufactured with a built-in factor of safety (FoS) that is normally around 7. A factor of safety indicates the difference between the rated load and the minimum breaking load of the equipment. This means that those 450 tonne rated slings, wouldn’t actually snap in a straight pull until at least 3150 tonnes, or 7 times that of the design load! So clearly those little fibres work.
Fibre slings were originally developed to lift objects where surface damage would be unacceptable. However, they can be used for any lifting operation where excess heat, certain chemicals, or unacceptable sharp edges are not present. They offer a huge advantage in weight savings over chains or wire rope making them safer to handle, as well as avoiding cuts and injuries from sharp edges or broken wires. These slings fail when lifts are not planned properly. There are many factors that can deleteriously affect the strength of a sling, these include, but are not limited to:
- Chemical damage
- UV damage
- Cuts and punctures
- Abrasion
- Embedded material
- Broken stitching
- Temperature damage
- Knots or hitches in the sling
- Inappropriate connectors
- Angle of lift
- Stability of load
- Sharp edges of load
- Overload of slings
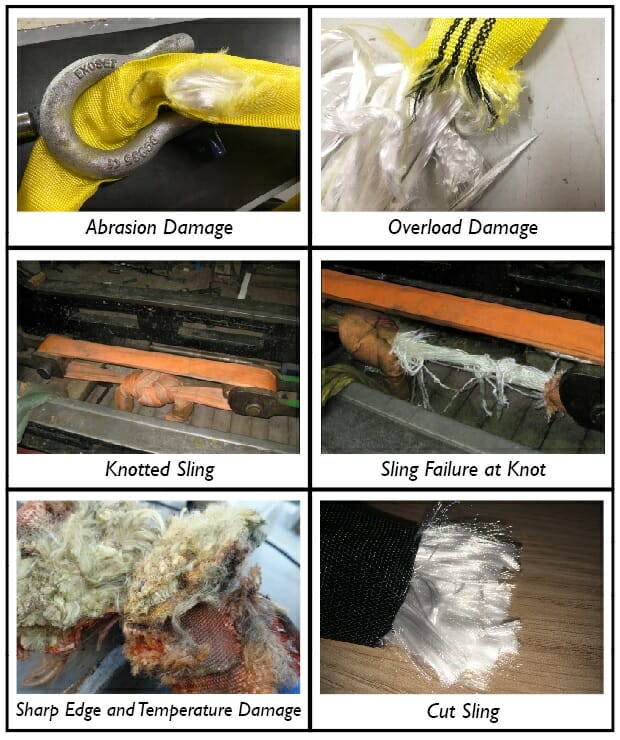
Sharp edges (either part of the load or near the load) are a serious concern in any lifting operation, regardless of the type of sling used. In fact, the definition of a ‘sharp edge’ was originally devised for wire rope. An edge is defined as ‘sharp’ if the edge radius (r) is smaller than the thickness of the sling (d); the thickness of the sling is defined as its thickness under load. However, consideration must also be given to the shape and structure of the edge itself, which may increase the sharpness of the edge.
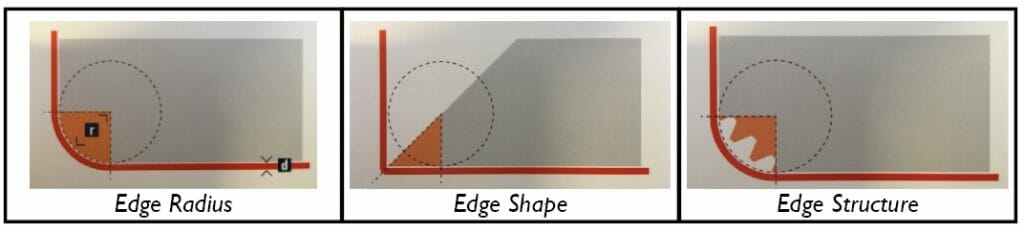
This rule means that an edge may be considered ‘sharp’ even if it’s a perfectly round object. For example, one available type of 100 tonne rated sling has a loaded thickness of approximately 35 mm. This means that any edge with a radius of less than 35 mm would be considered ‘sharp’ – that’s the size of a cricket ball, not something you would normally consider sharp!
Hawkins has been conducting independent investigations for nearly 40 years and employs a team of experienced and qualified scientists and engineers. A number of the team are familiar with the different characteristics of lifting procedures, legislation, method, and materials examination in order to determine root cause of failures. Please contact a member of the team to discuss the range of services that we can offer.