A Fibre Reinforced Polymer (FRP) composite, is a composite material wherein a polymer is reinforced with fibres. An FRP composite is made of two or more materials, one that forms a continuous phase (i.e. resin matrix) and a secondary material that acts as reinforcement (i.e. continuous or short fibres). it is necessary to have the reinforcing material fully encapsulated by the matrix. As such, an engineering composite is considered a heterogeneous material, i.e. constructed of two or more distinct constituents/phases.
Their excellent properties have seen them become an appealing engineering material due to their high strength-to-weight ratios, high modulus (only slightly changing shape under elastic load), magnetism and corrosion resistance. The fibres used include carbon fibre, glass fibre, boron fibre, and aramid fibres, which can be either continuous or short fibres. The resin matrices used are mainly thermosetting resin and thermoplastic resin.
A single layer of fibres embedded with resin is called a lamina, and a composite part is made of stacking many of these laminas on top of one another, in different directions/orientations. Generally speaking, fibres are aligned in the direction of the load in the structure. Consequently, FRP composite structures are highly tailored structures whereby the fibre direction and the number of laminas at each location of the structure, can impart specific strength and stiffness requirements. This tailored approach and the high strength of fibres compared to some homogeneous materials (e,g. steel), provides significant weight-saving benefits for the composite structures.
Composite Manufacturing Methods
There are several different methods for manufacturing composite parts, however, they tend to fall into one of two groups:
- Use of dry fibres and addition of the resin in the process of manufacturing
- Use of pre-impregnated fibres (prepreg)
The manufacturing cost for methods using dry fibres is normally lower than those using prepreg. However, parts made from prepreg normally have a higher fibre volume fraction (i.e. the number of fibres in a defined volume of composite).
Some of the methods using dry fibres and resin include;
- Wet layup
- Vacuum infusion
- Resin transfer moulding (RTM)
- Vacuum-assisted RTM
- Braiding
Examples of prepreg methods incude;
- Filament winding
- Tape placement
After producing the shape required for the part (or getting as close as possible to it) the resin matrix needs to be cured. Curing results in the solidification of the resin, which enables it to keep its shape after being removed from the mould. The curing process is a chemical reaction involving the cross-linking of polymer molecules, which ultimately solidifies the polymer. The crosslinking speed has a direct relation to the energy provided to the resin, hence most of the parts are subjected to heat to cure the resin in a reasonable length of time.
The layered structure of composites also means that the quality of the part can be heavily influenced by the manufacturing process and machinery used. Any wrap or wrinkle in fibres and/or misalignment in the fibres before the structure is cured will reduce the load bearing capacity of the structure. The introduction of contaminants, such as dust particles, between the layers at the time of manufacturing may also compromise the mechanical integrity of the composite, resulting in a defective structure.
Composite Failure Modes
Composite materials derive many of their advantages from their anisotropy (different directions of fibre within the matrix structure). However, this feature also gives rise to complicated three-dimensional states of stress at cut-outs, notches and cracks. Another factor that makes the description of composite failure difficult is their heterogeneity. In other words, the composite is made of individual ply, which themselves are composed of different fibres and matrix. Thus, when a global failure occurs, the propagation of any damage occurs via a mechanism that is only similar to a crack in the global sense. Some of the failures seen in composites are;
- Matrix cracking
- Fibre breakage
- Debonding
- Transverse-ply cracking
- Interface cracking
In composite failures, it is rare to come across one single failure mode, and in most cases, the failure is a combination of the modes listed above. In addition, due to the layered structure of FRP composites, the failure may not be visible on the surface of the part, or the visible damage may be much smaller than the actual fault inside the structure. A good example is impact damage. In these cases, the surface may present a very small indentation, sometimes barely visible to the naked eye. However, the delamination produced beneath the surface would be larger in size and depth by several orders of magnitude.
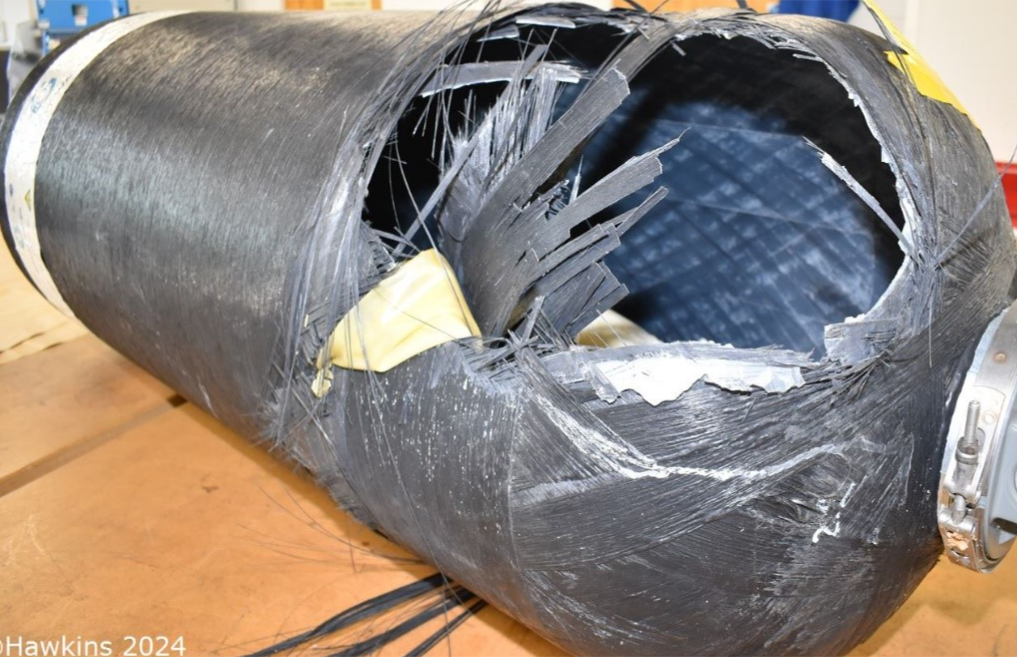
Composite Failure Investigation
To conduct failure analysis on composite materials, not only do we need to consider the heterogeneity and directional nature of the material itself, but also their compatibility with the environment the part was working in. For example, some polymers degrade because of exposure to UV and become brittle over time. This in turn will ease crack propagation in the structure and may also further expose the fibres to the environment.
Design details of composite structures such as the location of the cut-outs and holes, ply drops and corners, play a vital role in defining the areas of stress concentration and those that are susceptible to damage initiation.
Other details such as the manufacturing method, installation/service history and geographical location of the component, are all important factors that need to be considered and understood thoroughly before a determination of the failure can be reached.
As with any forensic investigation, the preservation of evidence is critical, and the failed part containing any fracture surfaces must be retained and kept safe until it can be examined. The most vital source of information, as with the failure analysis of any engineering material, is the area in which the crack initiated and propagated.
Composites are relatively brittle materials and contact between fracture surfaces after failure can result in losing important forensic detail due to abrasion, and therefore special attention needs to be given to ensuring the integrity of the fracture surfaces post-failure.
About the Author
Materials engineer, Dr Amir Hajdaei has extensive experience in dealing with a wide range of materials including metals and ceramics and has an in-depth knowledge of fibre reinforced composites and polymers.
After completing his PhD at the University of Manchester, Amir worked as a principal composite engineer, testing composite materials and parts for wind, oil and gas and aerospace industries. This made use of his knowledge of the mechanical properties of fibre reinforced composites and specialism in time-dependent properties, such as fatigue and creep/stress rupture.
With over fifteen years of experience working on fibre reinforced composites, polymers and adhesive bonded joints, Amir has a thorough understanding of composite manufacturing methods, as well as composites and polymer failure mechanisms.
If you have a materials failure that you would like Amir, or any of our other materials engineers to investigate, get in touch.