Hydro Power
Hydro power generation was the first green renewable energy and battery storage facility. The size of hydro plant can vary from less than a 100kW to over 30 MW per unit. The design comes in three types:
- Impoundment: Dams store water in a reservoir and the stored energy can be released on demand, for example the Hoover Dam.
- Diversion: Run of the river water is diverted to pass through a turbine which is less costly and less intrusive to the local environment.
- Pumped Storage Hydropower (PSH): A penstock and turbine hall connects two reservoirs. Water can be pumped from the lower reservoir to the top reservoir during low-demand periods so that it is ready to be used when needed.
The design is robust and due to the low rotational speeds of 80 to 350 rpm, the stresses can be low. This results in a long service life with some hydro plants operating successfully for close to a hundred years.
WHY APPOINT A FORENSIC INVESTIGATOR?
Hawkins forensic investigators have completed numerous investigation into hydro power plant failures.
Major inspection intervals can be long, typically 25 years, so a station engineer may be involved in at most, two major inspections depending on the number of units at the facility. Our experts are familiar with the different components and have the experience to complete an assessment that the operating team may not have.
Problems are often a result of ingestion of debris which causes impact damage. Issues can also arise due to the age of the units. During inspection, it is possible that they contain a significant number of defects which a repair shop may try to repair. As these may be casting defects, this itself can lead to further issues.
Hawkins have found that many of these can be related to original manufacturer defects which have not propagated and are therefore dormant. Undertaking a repair to these ‘non-defects’ can generate further cracking due to the age of the components and the materials not being as clean as modern-grade steels.
Having an experienced investigator on the team can reduce the risk of repair vendors rushing into repairs that are not required.
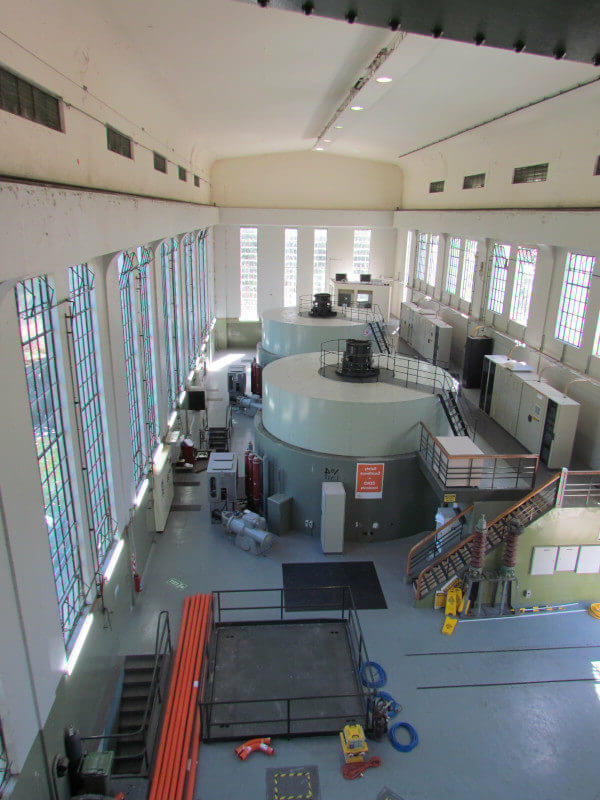
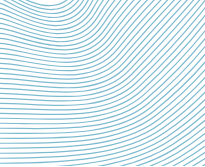
Examples of Typical cases
The list below provides a few examples of cases which we investigate regularly or have investigated in the past.
- Wicket gate failures
- Penstock degradation/condition assessment
- Generator failures
- Bearing failures
- Pressure problems, such as too high or too low pressure or ‘water hammer’ issues.
If you would like to discuss how we can assist you please fill out our enquiry form or call us for a free consultation.
HOW DOES HAWKINS INVESTIGATE HYDRO POWER PLANT FAILURES?
When Hawkins is requested to investigate an issue we employ in-house methodology built from over 40 years of experience. This enables all Hawkins investigators to provide a consistency of service and product. The methodology comprises three steps:
1
Consultation
On receipt of the enquiry, we discuss with the instructing party what happened, when it happened and request a suite of data covering the operation and maintenance of the asset during its operating life. This collected data may include video coverage showing the operating conditions present in the plant prior to, and during the event. We also interview personnel present at the time of the event to get an insight into the timeline of events before, during and after the event.
2
Inspection
Following collection of all the data and completion of the consultation, Hawkins engineers will visit the site or repair shop to inspect the asset. This will enable us to assess the extent of the damage and identify the source of the failure. This step can be completed on-site or may require samples to be removed and examined in one of Hawkins’ laboratories.
3
REPORTING
On completion of the inspection, a detailed report will be issued summarising the work completed and the findings of the investigation. This can include advice on operational and inspection changes to implement to minimise future events if relevant.
SPEAK TO ONE OF OUR EXPERTS
Testimonial
“Thank you for your superb effort in this case.”
Rhys Phillips
“Many thanks for turning out today at such short notice and providing the benefit of your expertise and knowledge. It was evident the Client was extremely relieved that this matter was being investigated expeditiously.”
Chaz Winterton
“I just wanted to say thank you for all your help and the information you found was of real insight. Thank you again for all your help.”
Stewart Hargreaves
“I just wanted to say thank you for all of your hard work preparing the Hawkins report. Please pass on my thanks to the rest of the team. We really appreciate the hours you have all put in and I know the client is pleased with your work.”
Philippa Jones
Related areas of expertise
Power & Energy
The world of power and energy has been undergoing fundamental changes in recent years following the increasingly rapid global paradigm shift away from the ‘traditional’ large fossil fuel power stations towards the ‘new world’ of renewable power and distributed or embedded generation.
Drains, Sewers & Septic Tanks
Few of us like to think too much about how wastewater or surface water run-off from their home, workplace or business gets to a place of treatment and/or safe disposal to the environment. But, when the infrastructure that either transports or treats this water fails, the resultant problems can be unpleasant, costly to rectify and damaging to the environment.
Flooding & Hydrology
Flooding is the most significant disaster risk in the UK. Flooding is estimated to cost the economy about £1 billion per year. More frequent, more intense storms resulting from climate change, and inappropriate developments in floodplains will put more people and property at risk in the future and will increase the impact of flooding. It is projected that the annual cost of flooding could be up to four times higher by the end of the century.
Chemical & Process Engineering
Chemical Engineering and Process Engineering are essentially interchangeable terms, whether it is engineering chemistry to make a desired product on the industrial scale for example a pharmaceutical drug or a beer or simply process materials for some beneficial purpose for example in water treatment or renewable power generation.